Newsroom
UBH auf der Common / POW3R 2024 – Zukunft mit IBM i gestalten!
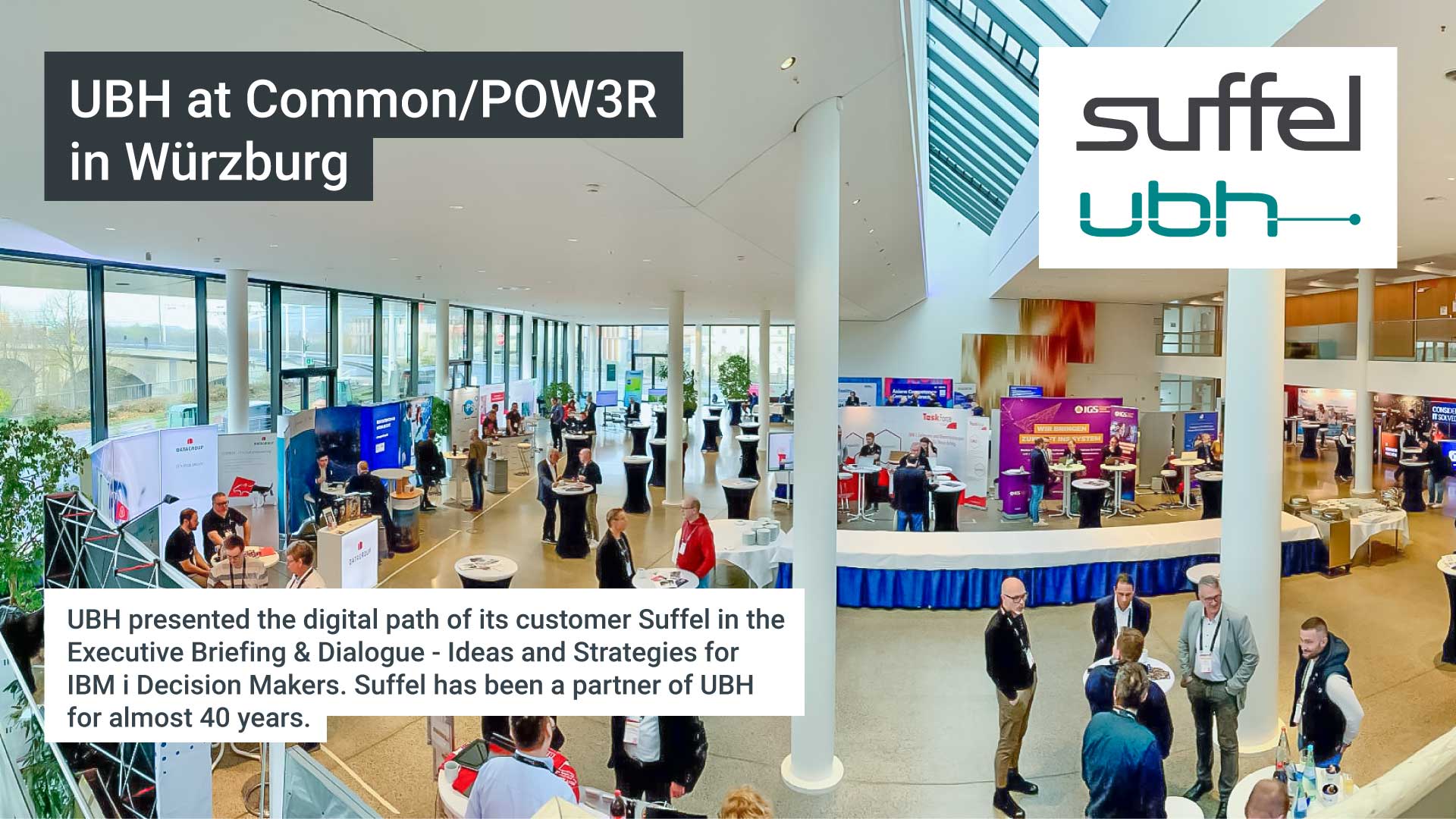
The future with IBM i – Successful digital transformation with UBH at the Common/POW3R 2024
In today's digital world, a future-proof IT infrastructure is the key to a company's long-term success. But what does ‘future-proof’ mean in the context of IT? And how can a powerful platform like IBM i help companies achieve their goals? These questions were at the centre of our presentation at Common / POW3R 2024 in Würzburg, where, together with our long-standing partner Suffel, we gave an exciting insight into the company's digital transformation process.
Looking back and ahead: Suffel's journey into the digital future
Suffel's journey began back in the 1980s with IBM i as the basic platform for its first IT applications. Since then, the company has continued to evolve, also backed by our in-house development, the ERP system wEBV, so as to meet the ever-growing complexity and demands of the market. Today, Suffel and UBH demonstrate just how a fully integrated IT solution can cover and optimise all corporate business processes.
At Common / POW3R 2024, together with Suffel, we presented the road map towards a modern IT platform in the Executive Briefing & Dialogue. From the first, straightforward applications in the 1980s to the powerful, comprehensive IT infrastructure of today - the digital journey at Suffel and of our wEBV system represents a perfect example of how all business processes can be transformed successfully.
Our customised ERP solution wEBV shows just how a fully integrated ERP system with powerful add-ons completely covers Suffel's company-specific requirements. Our solution is flexible and scalable so that it can grow with the company - an important factor for the future digital viability of your company.
What makes the solution from UBH and IBM Power so unique is its high degree of digitalisation - a development that not only optimises internal processes, but also enhances customer experience, thus contributing to the long-term success of the company.
State of the art with wEBV & IBM Power: the technological foundation for the future
Our wEBV solution is based on the tried-and-tested IBM Power platform, which acts as the central hub for all business processes. With the integration of modern app applications and a user-friendly interface, we have created a solution that is not only efficient but also intuitive to use.
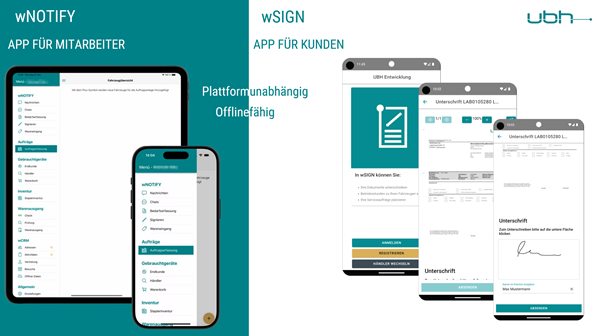
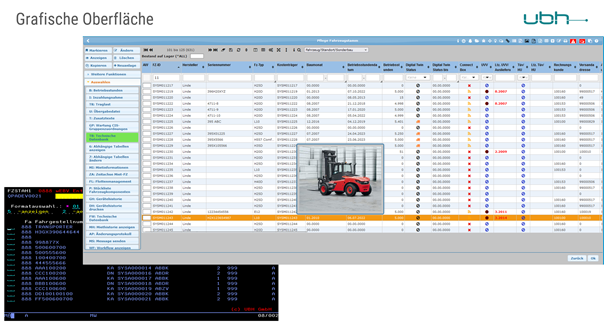
Why a modern IT platform is so important
Digital transformation is not just a short-term trend, but a long-term necessity. In times of big data, cloud computing and artificial intelligence, companies need an IT infrastructure that is flexible, secure and powerful. wEBV offers precisely these advantages and enables companies to react quickly to market changes while retaining control over their data and applications.
It is clear to us that digitalisation is the key to success. But the real challenge is not only to implement the right technologies, but also to create a platform that can be evolved over the years.
What do you think? What role does a modern IT platform play in a company’s long-term success? We look forward to being able to share our mutual experiences and opinions with you. What challenges have you experienced with digitalisation in your company? Which technologies do you think are future-proof? Share your thoughts with us in the comments!
Find out more and get in touch
If you would like to learn more about UBH's solutions and our experience with the IBM Power platform, contact us directly! We look forward to showing you how your organisation can benefit from a modern, flexible and scalable IT infrastructure.
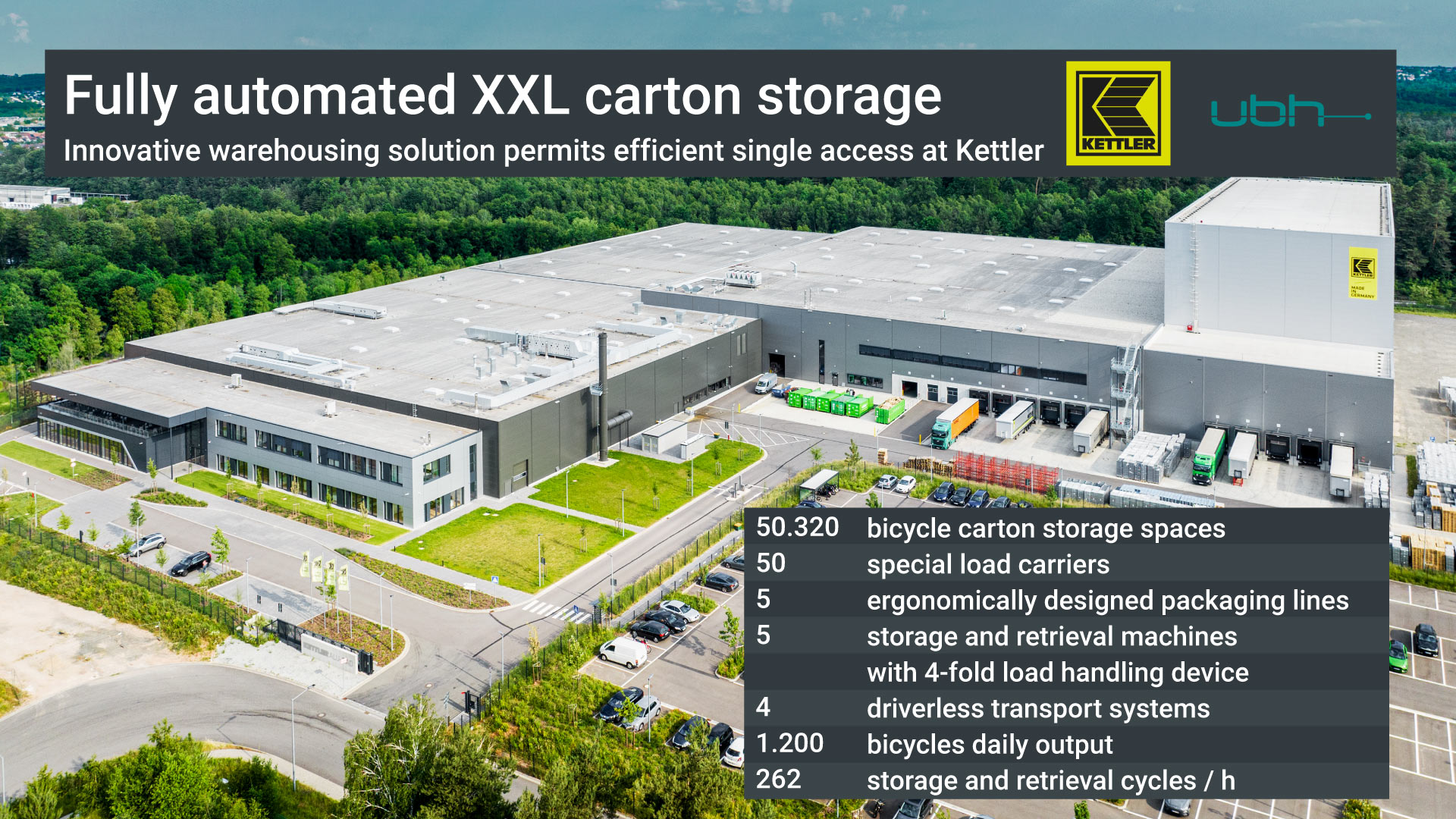
An investment of 100 million euros, an area encompassing 62,000 square meters, 300 workplaces - the KETTLER Alu-Rad bicycle plant in St. Ingbert, Saarland, is a commitment to Germany as an industrial location. UBH SOFTWARE & ENGINEERING has raised the efficiency of the plant’s intralogistics to the next level, in order to ensure that e-bike assembly Made in Germany is also worthwhile.
In St. Ingbert, `level´ does not merely mean category in terms of manufacturing. At the KETTLER Alu-Rad plant, `level´ also stands for a pioneering intralogistics solution which transforms available space into a highly efficient three-dimensional process structure. A pioneering role is played by UBH's handling system, which fully automates internal logistics processes - from packaging and transportation via storage, picking and loading of the bicycle cartons. After all, up to 1,200 bicycles have to be moved quickly and safely at the site every single day, this plant being one of the largest and most modern bicycle factories in Europe. This was achieved via intelligent interaction of IT and seamless material flows. UBH, as the general contractor, developed and implemented the entire information and control technology, special conveyor technology, driverless transport system, automated high-bay warehouse designed as a silo structure and its pre-zone building.
Challenge: high-mix-low-volume puts automation to the test
At the KETTLER Alu-Rad plant in St. Ingbert, process reliability is a central component of the intralogistics processes for finished goods. While assembly of the e-bikes still requires manual labour, packaging, internal transport, storage and retrieval, picking and dispatch are fully automatic. At the onset of the assembly process, the future bikes abandon their original terrain and take to the air. Suspended in a four-kilometre-long frame conveyor system installed on the ceiling, the frame finds its way fully automatically through the entire factory - from the paint shop to the four assembly lines with a capacity of over 500 e-bikes per day in single-shift operation. Packaging and automatic outfeed take place immediately downstream of each assembly line.
Automating the high-mix, low-volume product range of KETTLER Alu-Rad with different carton sizes requires a high degree of flexibility. UBH has found an innovative solution for this requirement, applying a UBH-own development which transports each individual bicycle carton vertically at floor level, records it in UBH’s LogiCS material flow control (MFC), subsequently collecting, strapping and closing it.
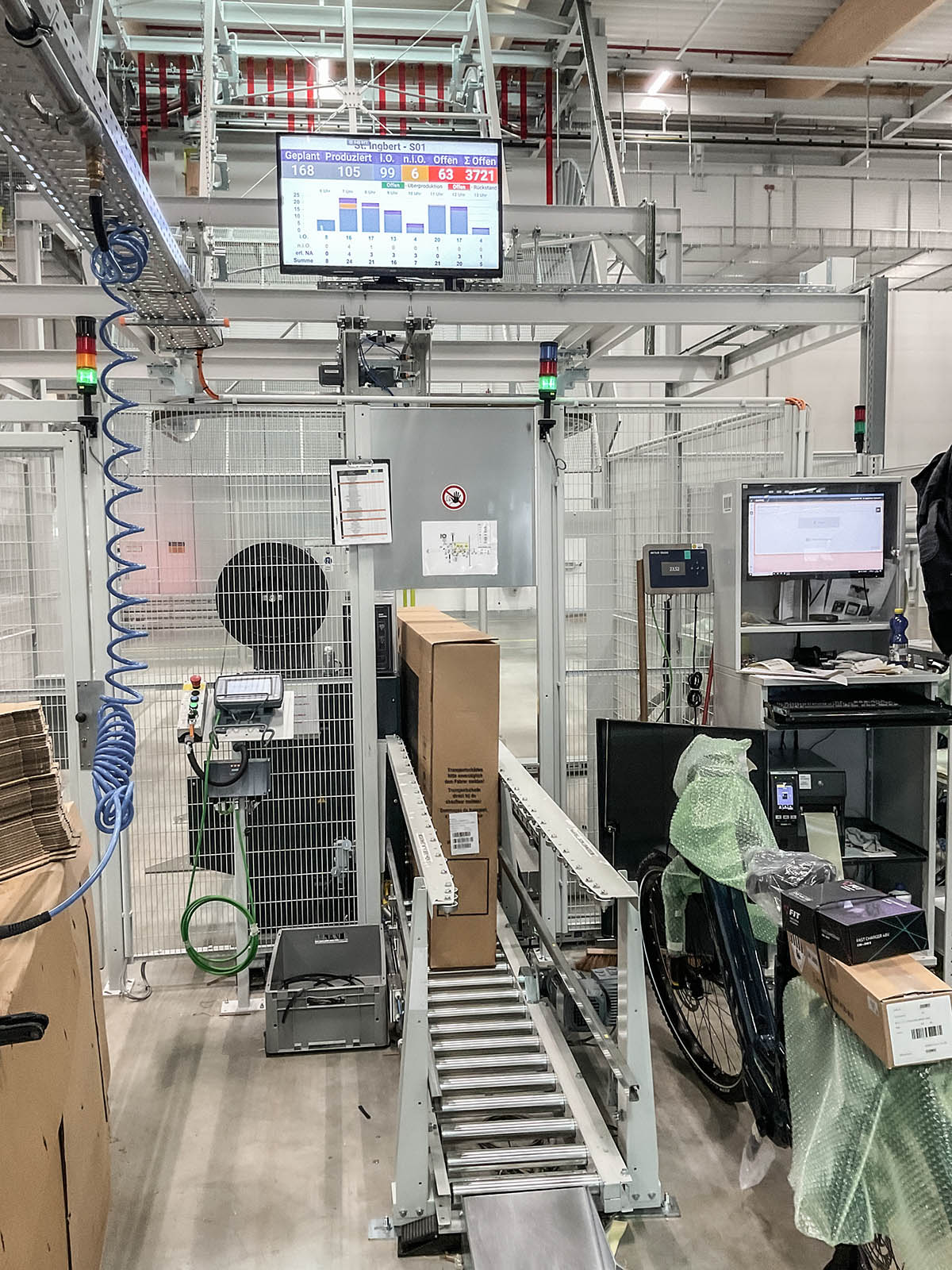
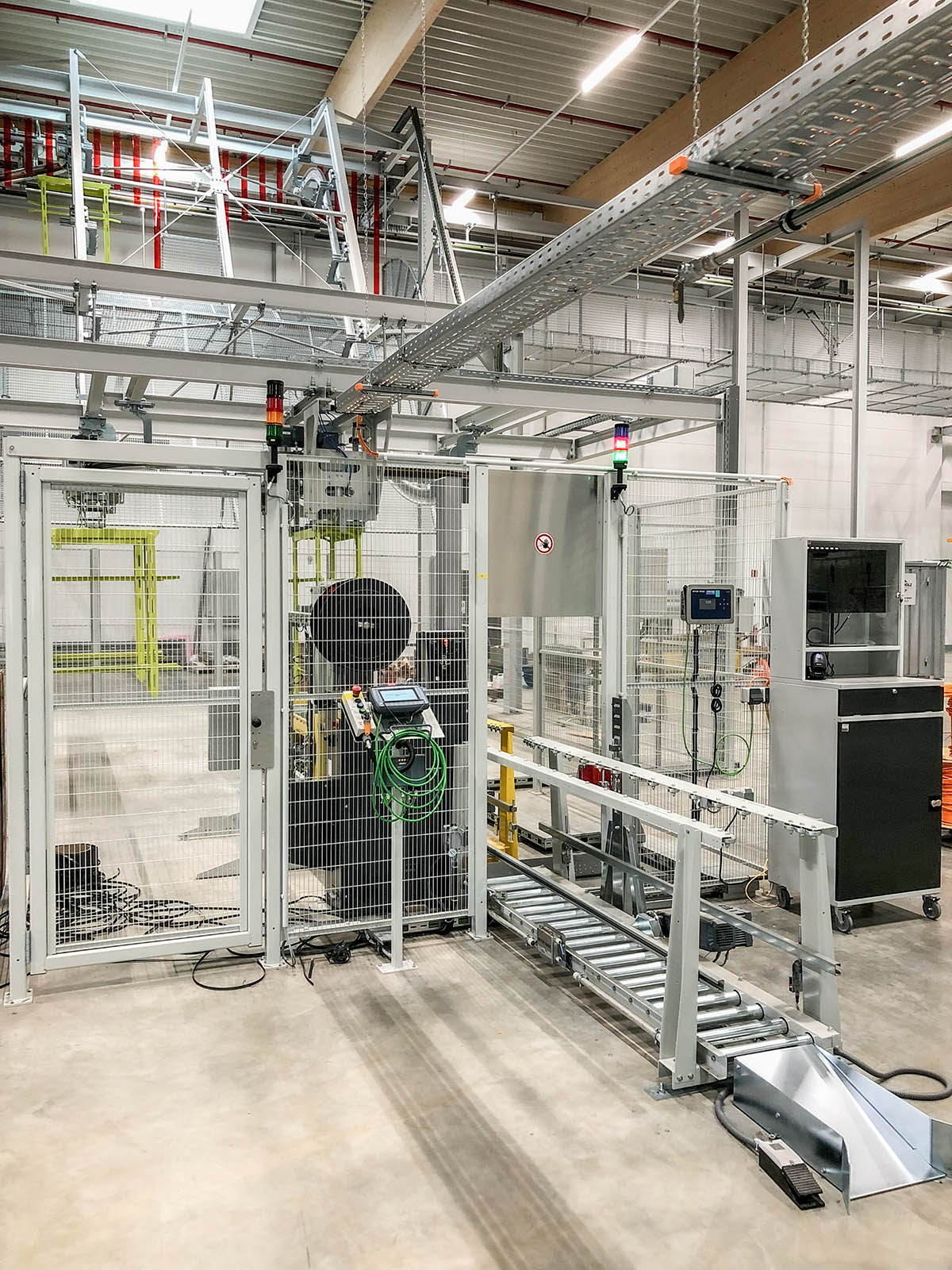
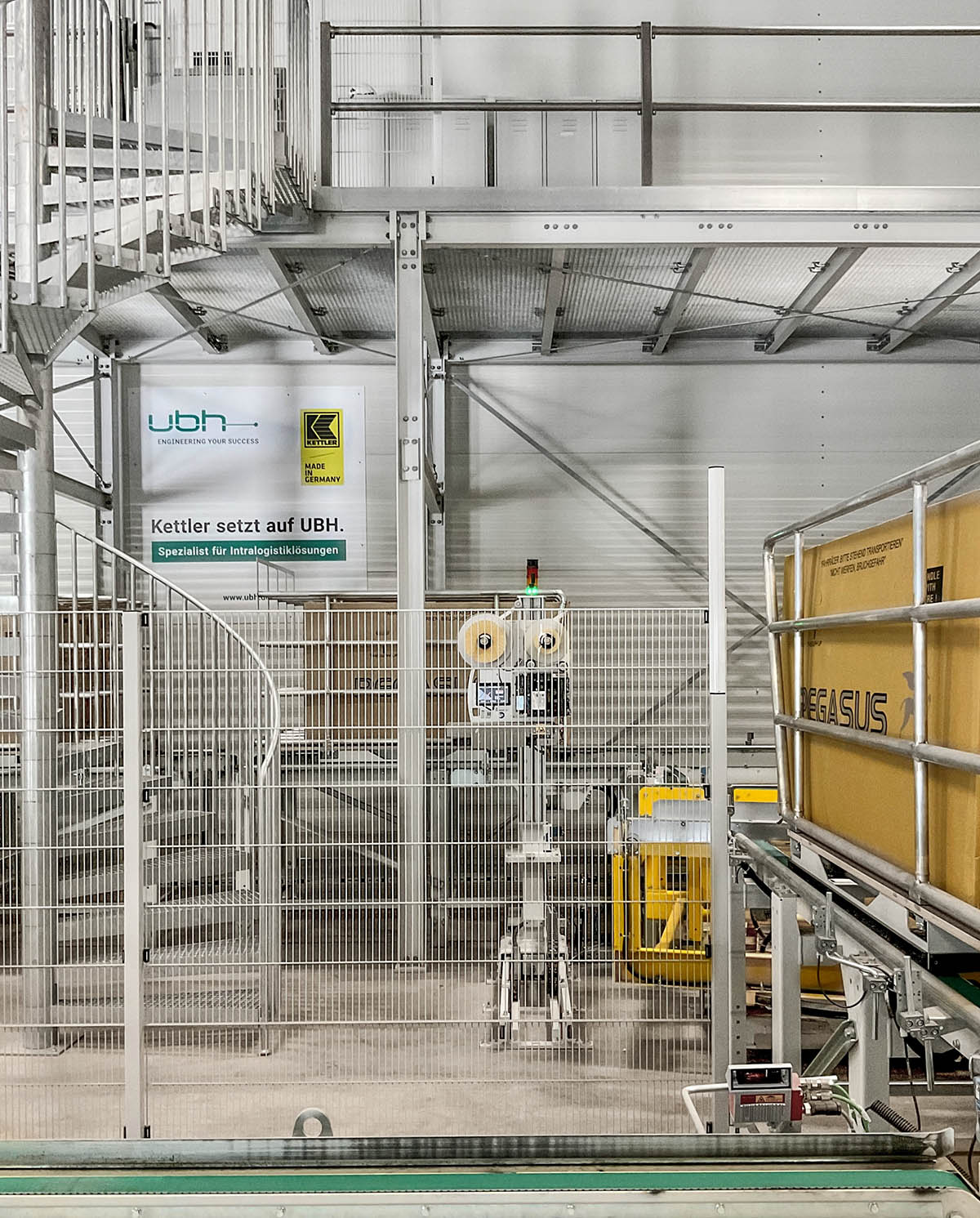
Assembly line
Preparations have been made for a fifth assembly line to increase capacity. All five conveyor lines are reversible and enable automatic removal and automatic supply of the bicycle cartons to the lines. In addition to KETTLER Alu-Rad, other brands belonging to the Zweirad-Einkaufs-Genossenschaft (ZEG) also benefit from this. In addition to Kettler, premium segments from BULLS, ROTWILD, Hercules, Zemo and i:SY are also assembled in St. Ingbert.
Adding value: bike transport at great heights frees up the shopfloor
At the end of the 7.5 m long pick-up and drop-off lines, the floor conveyor system transfers the bike cartons to an electric overhead conveyor system, bringing them to a transport level located below the nine-metre-high ceiling. As each of the five lines has its own transfer station, transport orders can be run independently of each other. Transport under the ceiling was also a major advantage in the factory planning phase: a free shopfloor floor represents increased added value. Obstacles such as finished bikes and possible damage are avoided, which could otherwise be caused by forklift trucks when transporting packaged bikes. This is still evident today in the factory’s flawless appearance, as Michael D'Erme, Plant Manager at KETTLER Alu-Rad, confirms: “After two years of production, the plant still looks as good as new.”
The overhead conveyor system is equipped with 20 gondolas for an hourly output of 150 individual journeys. Five production lines at floor level, a maintenance bay and a mezzanine floor at a height of 6.5 m are connected to the electrified overhead conveyor system. All three areas represent separate fire compartments and were equipped with special fire protection gates through which the gondolas travel.
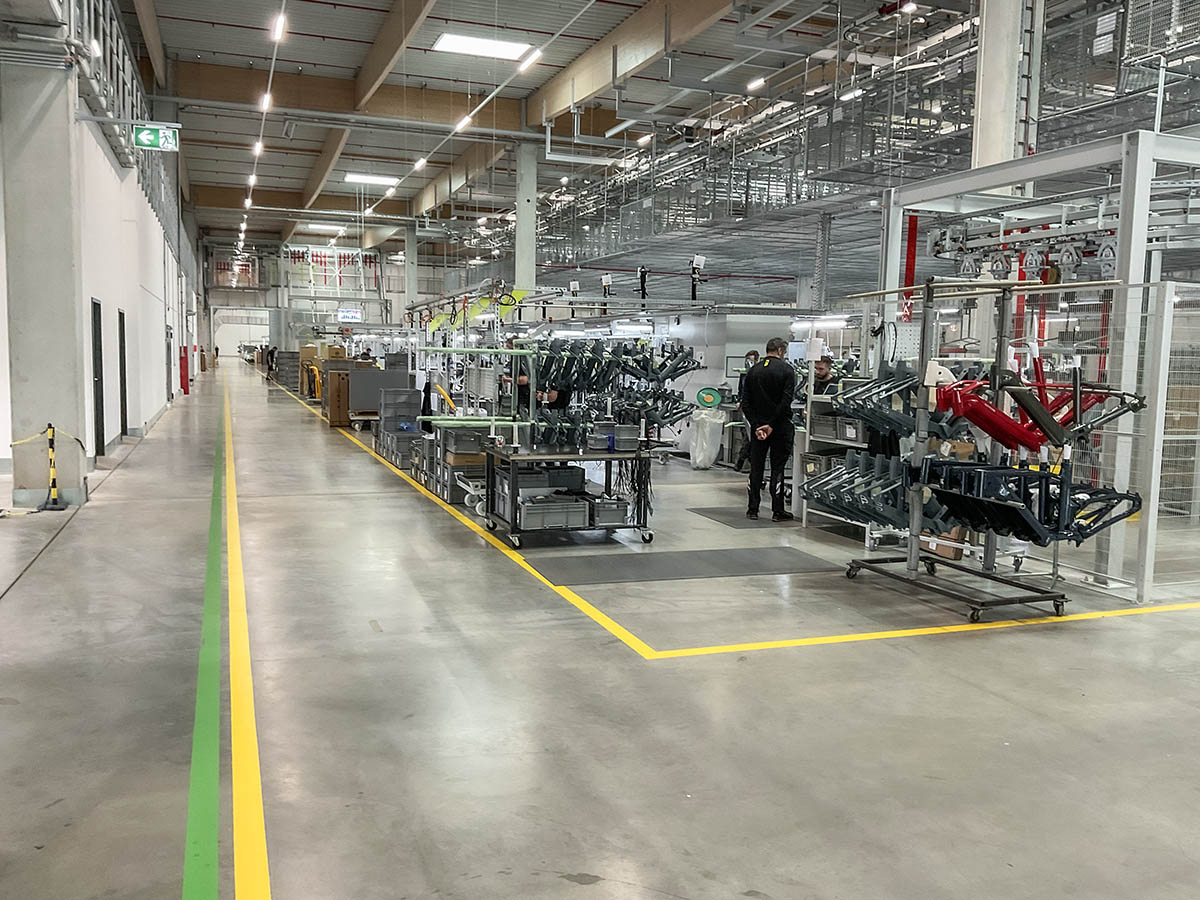
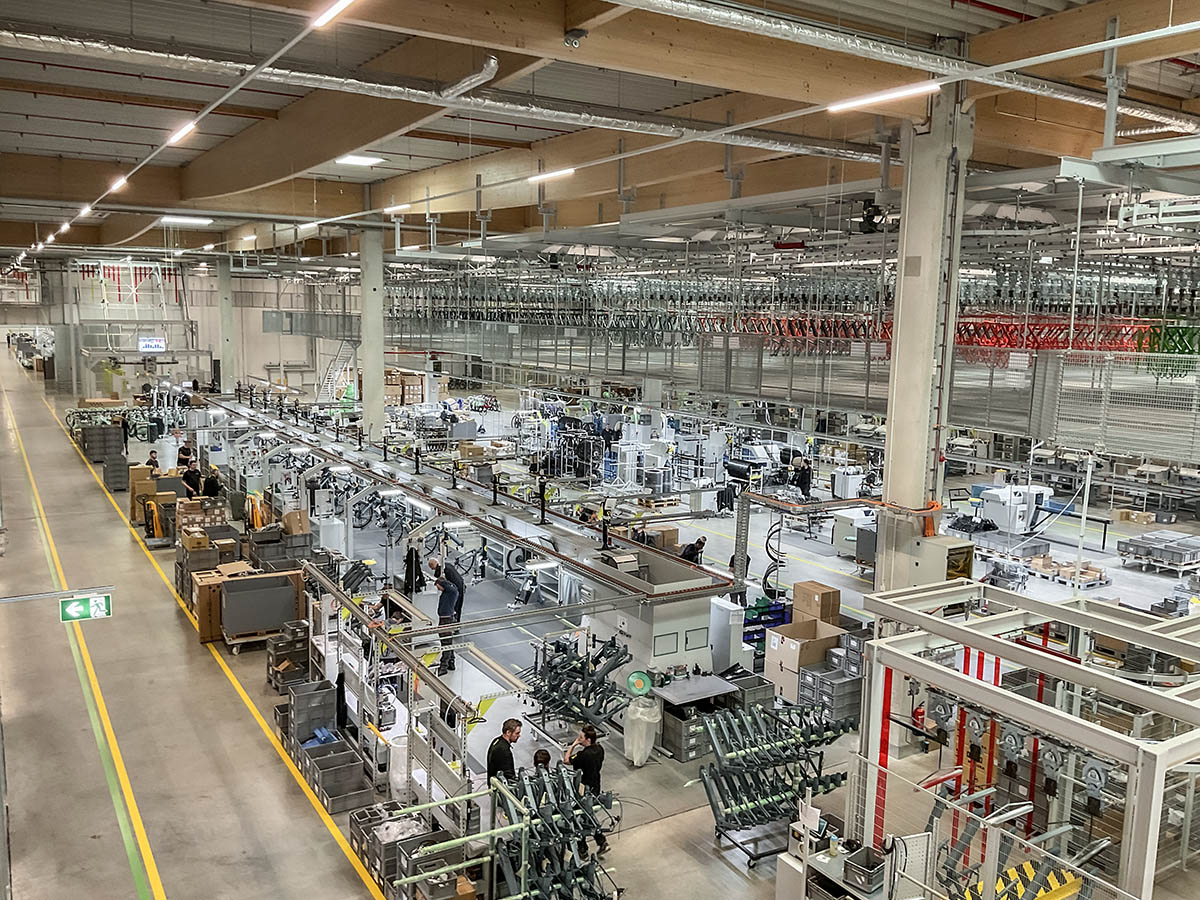
Shopfloor & Assembly line
Performance consolidation: decoupled processes for efficient material flow
The mezzanine connects the production area with the pre-zone to the high-bay warehouse over a length of 100 metres. The goods receiving area and the raw materials warehouse are located at floor level directly below. Two belt conveyors each transport four bicycle cartons on specially developed trays. This results in an increase in capacity on the conveyor line both in the inbound and outbound. The bicycle cartons are transferred automatically from the overhead conveyor to 4-fold trays and back. In order to decouple processes and enable a highly efficient material flow between production, the connecting section, the pre-zone and the high-bay warehouse, up to 20 trays with 80 bicycles can be buffered on the mezzanine, both on the infeed section and on the outfeed section. The handshake between the mezzanine and the pre-zone takes place via two vertical conveyors which transfer the trays to belt conveyors. As there are two fire compartments, an additional fire door was installed at this point.
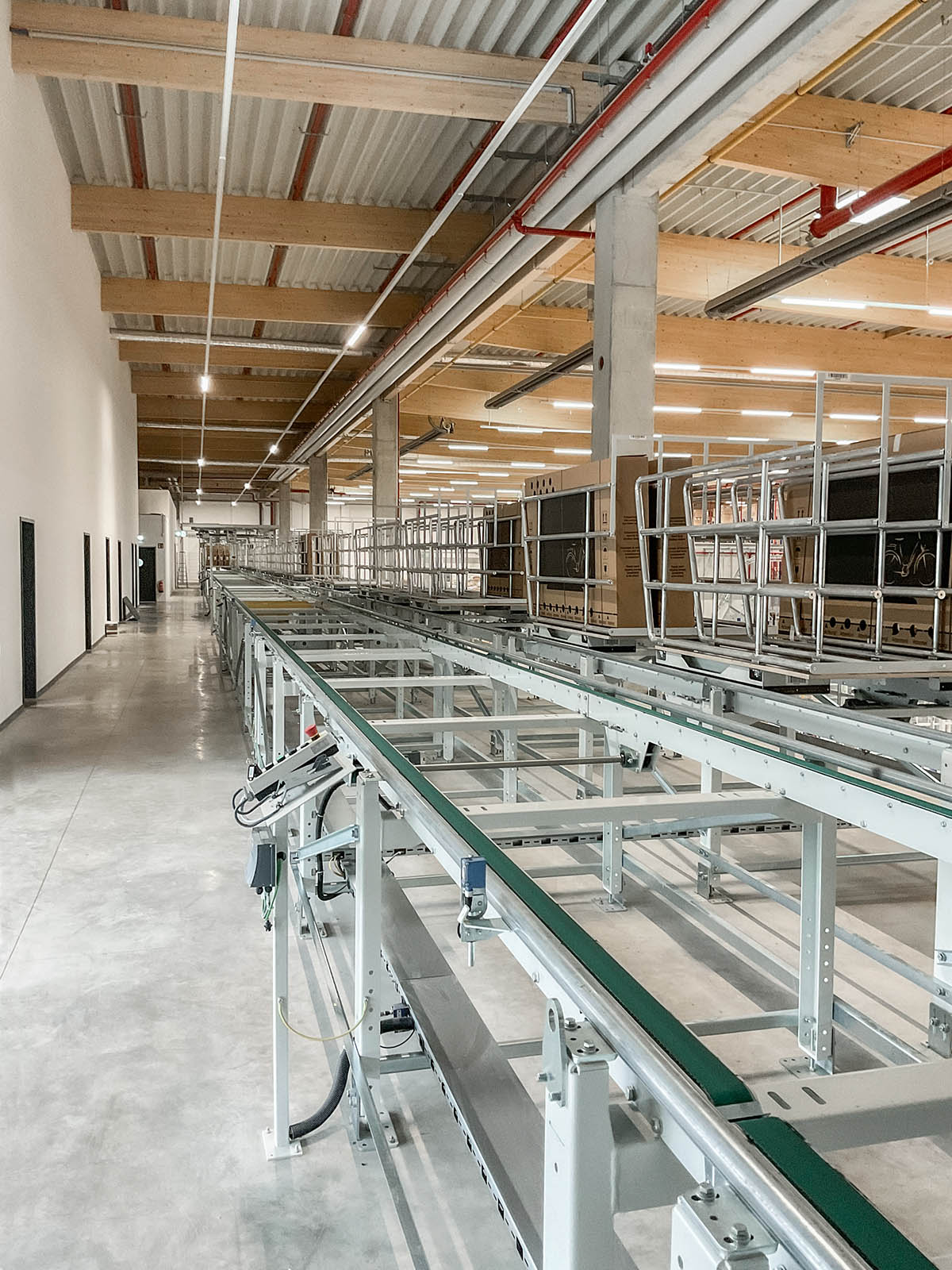
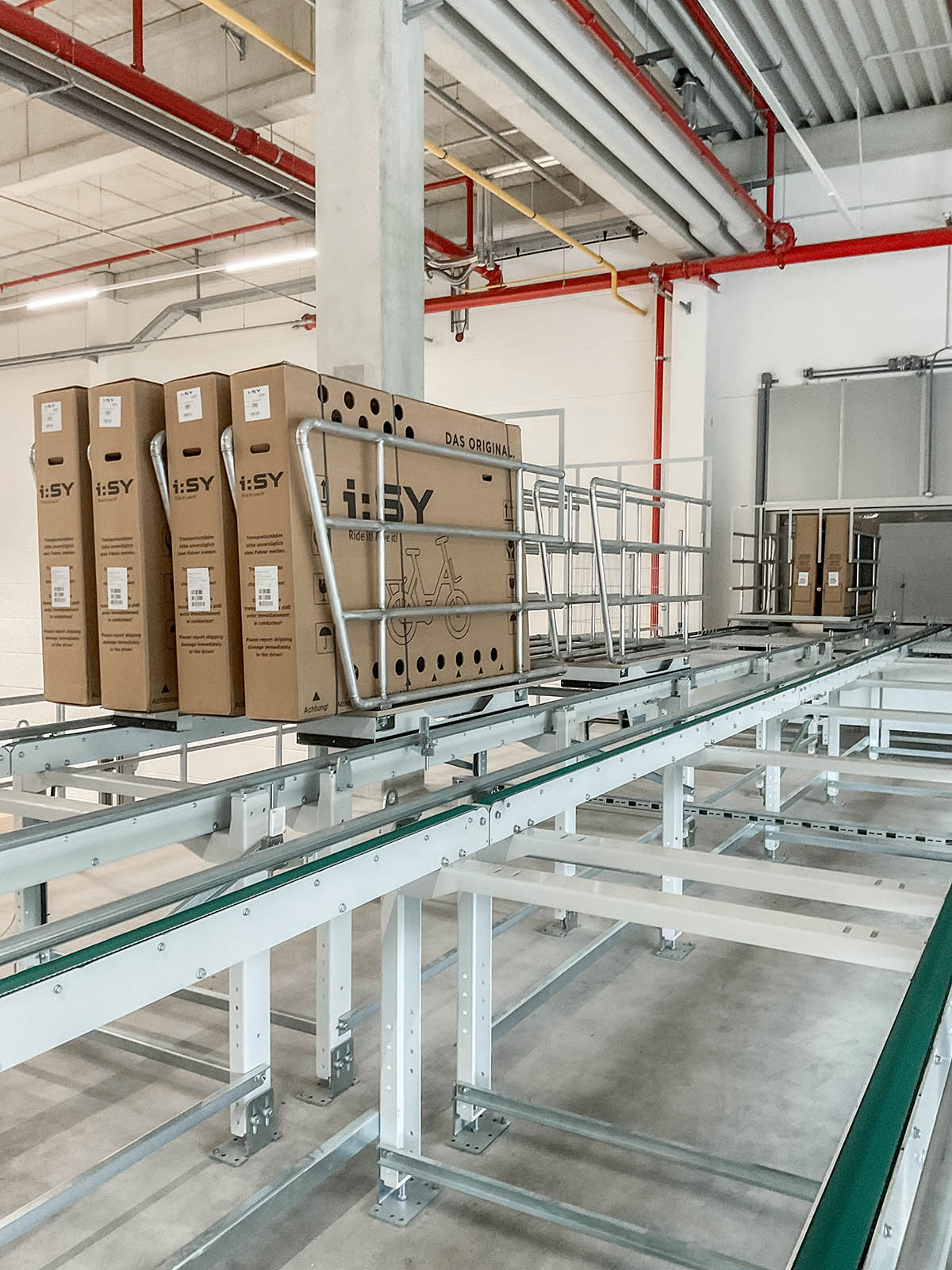
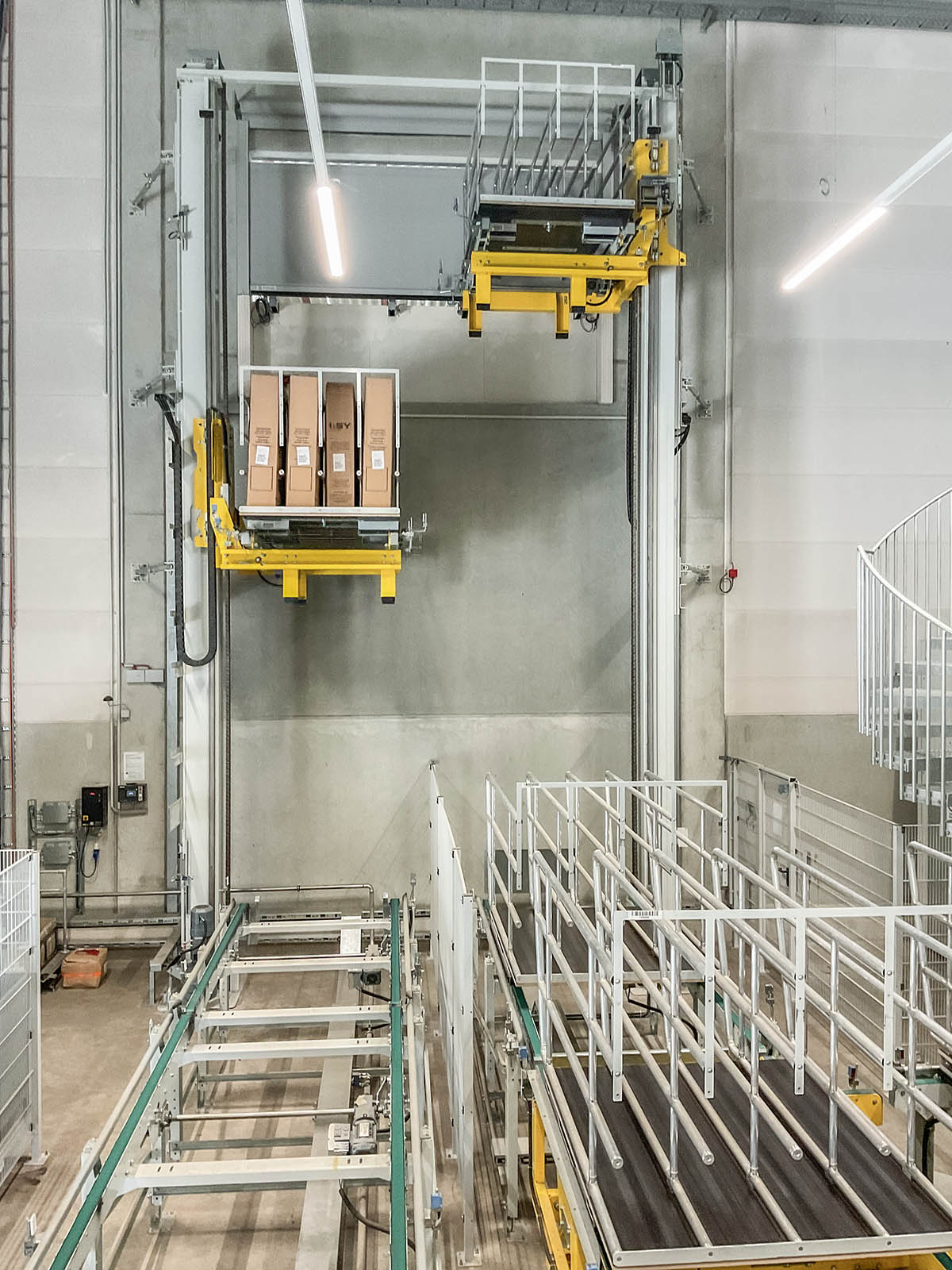
Conveyors at Mezzanine
Superlative: 50,320 e-bikes in the high-bay warehouse encompassing 107,000 m³
The high-bay warehouse and the pre-zone were designed as a silo structure and were part of UBH’s delivery scope. The pre-zone, which is 35 metres wide, 18 metres deep and 14 metres high, forms the logistics centre where all material flows of finished goods with a daily output of 1,200 bicycles come together. Material flows from production, the high-bay warehouse and the docking gates move inbound and outbound at the same time, running parallel in both directions and thus avoiding bottlenecks. Five docking gates in the gable wall open up to the adjacent truck bays. A fully automated pre-zone measuring 630 m² features access to the maintenance areas and high-bay warehouse for staff and visitors via a look-out platform 4.5 metres high, 29 metres wide and 3 metres deep.
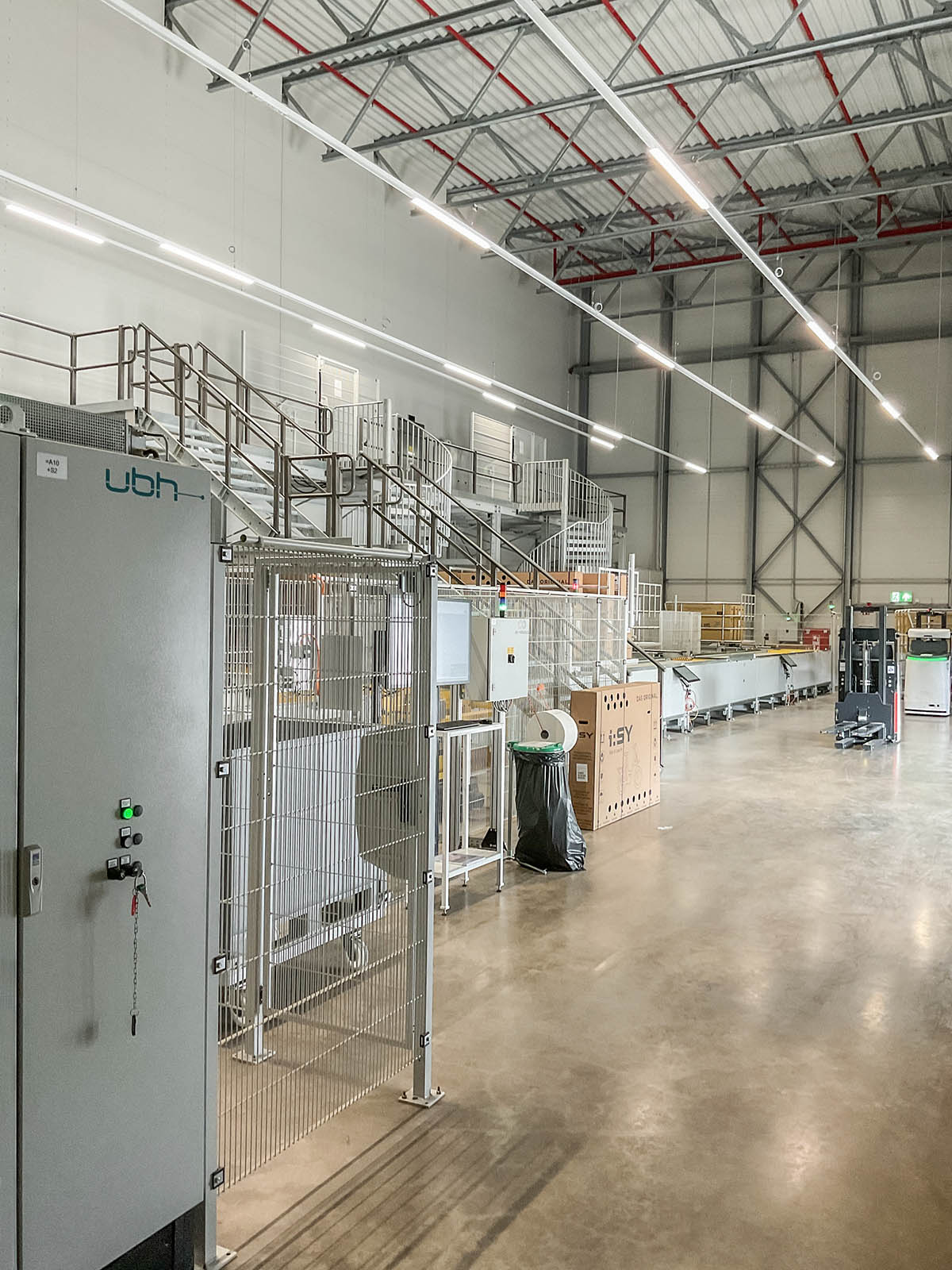

The hermetically sealed high-bay warehouse is also a real superlative, offering space up to the ceiling for 50,320 e-bikes with individual access. In total, the warehouse has a volume of 107,000 m³ with 31 metres aisle height and 96 metres aisle length. The racking system specially developed for KETTLER Alu-Rad is spread over five aisles and can store each bicycle box individually without a tray. Transport in the high-bay warehouse is handled by five storage and retrieval machines with a storage and retrieval capacity of over 260 cartons per hour. But that is not all. The high-bay warehouse can do more than merely store and retrieve bicycle cartons. An additional highlight is the fully automated order picking feature. For this purpose, each storage and retrieval machine is equipped with a specially developed quadruple load handling device. Thanks to the introduction of this new technology, KETTLER Alu-Rad is capable of picking bicycle cartons fully automatically and thus providing a zero-error guarantee when fulfilling customer orders.
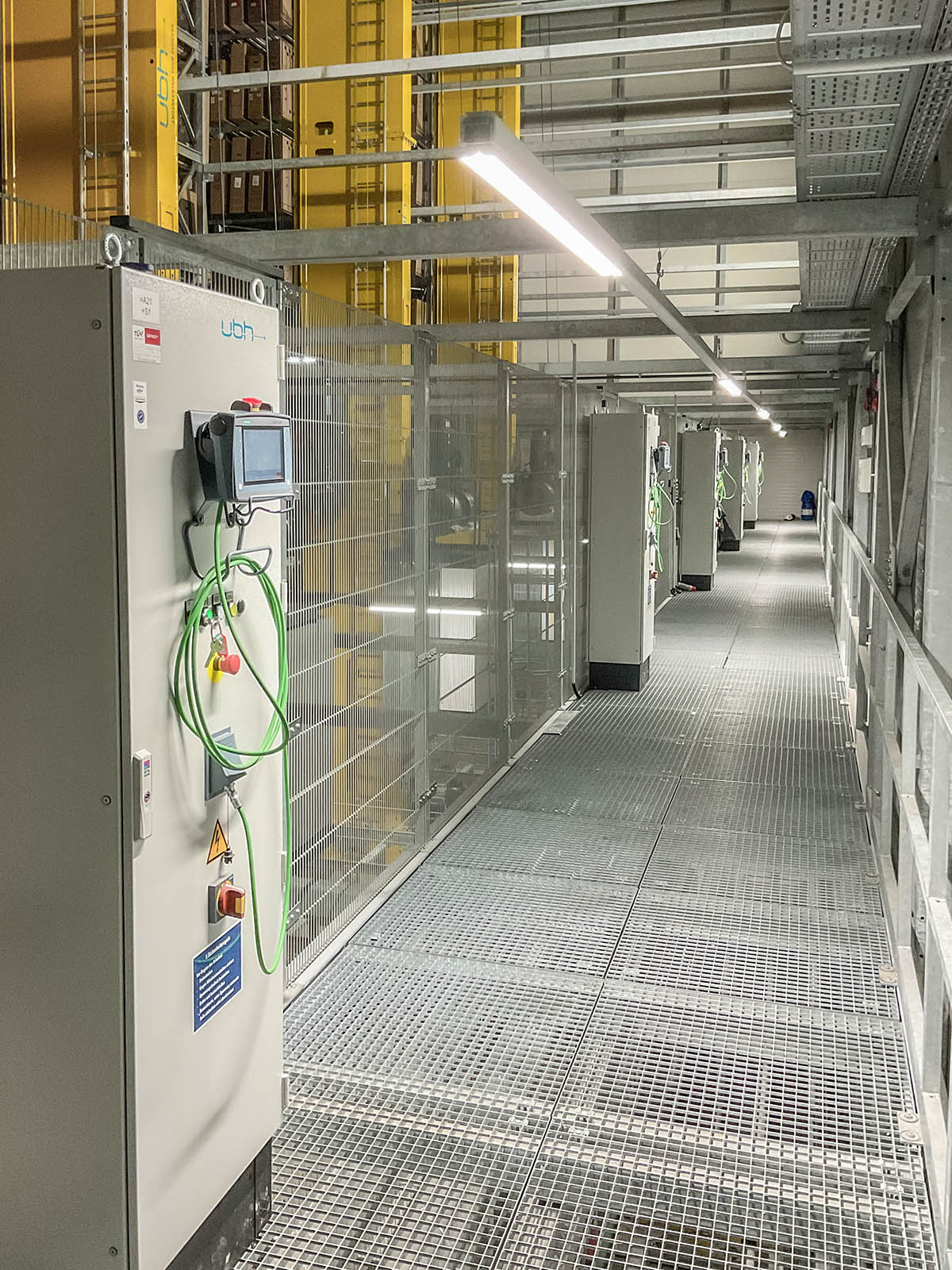
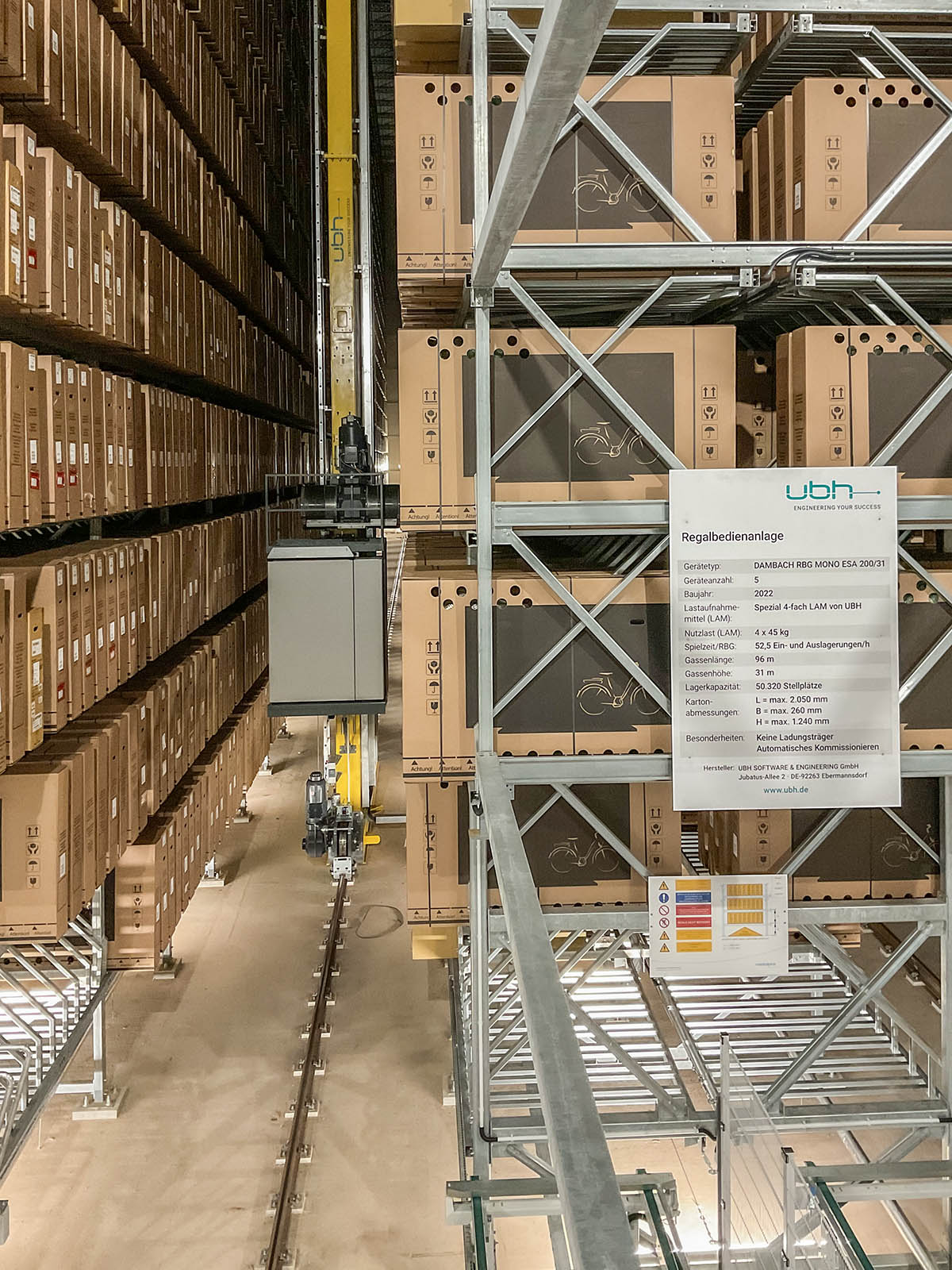
Seamless: Fully automated intralogistics right to the truck
Following automatic picking, the 4-fold load handling device transfers the bicycle cartons to empty trays which are controlled by UBH’s LogiCS material flow control and are ready at the conveyor loop just-in-time. A total of two storage and retrieval stations for trays in the new distribution centre at KETTLER Alu-Rad are connected to the network of storage and retrieval devices and conveyors. Before the bicycle cartons are loaded onto the truck, shipping labels being added by two automatic labelling stations.
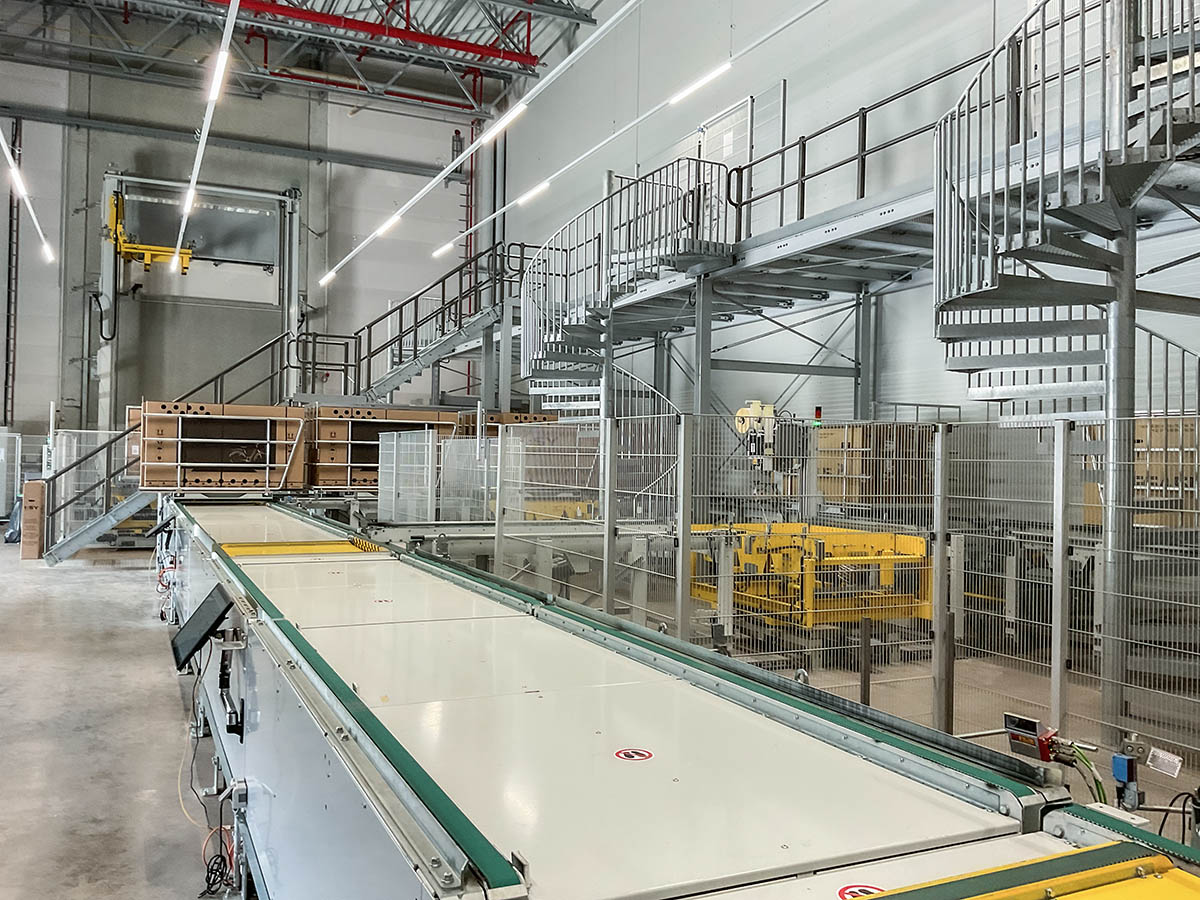
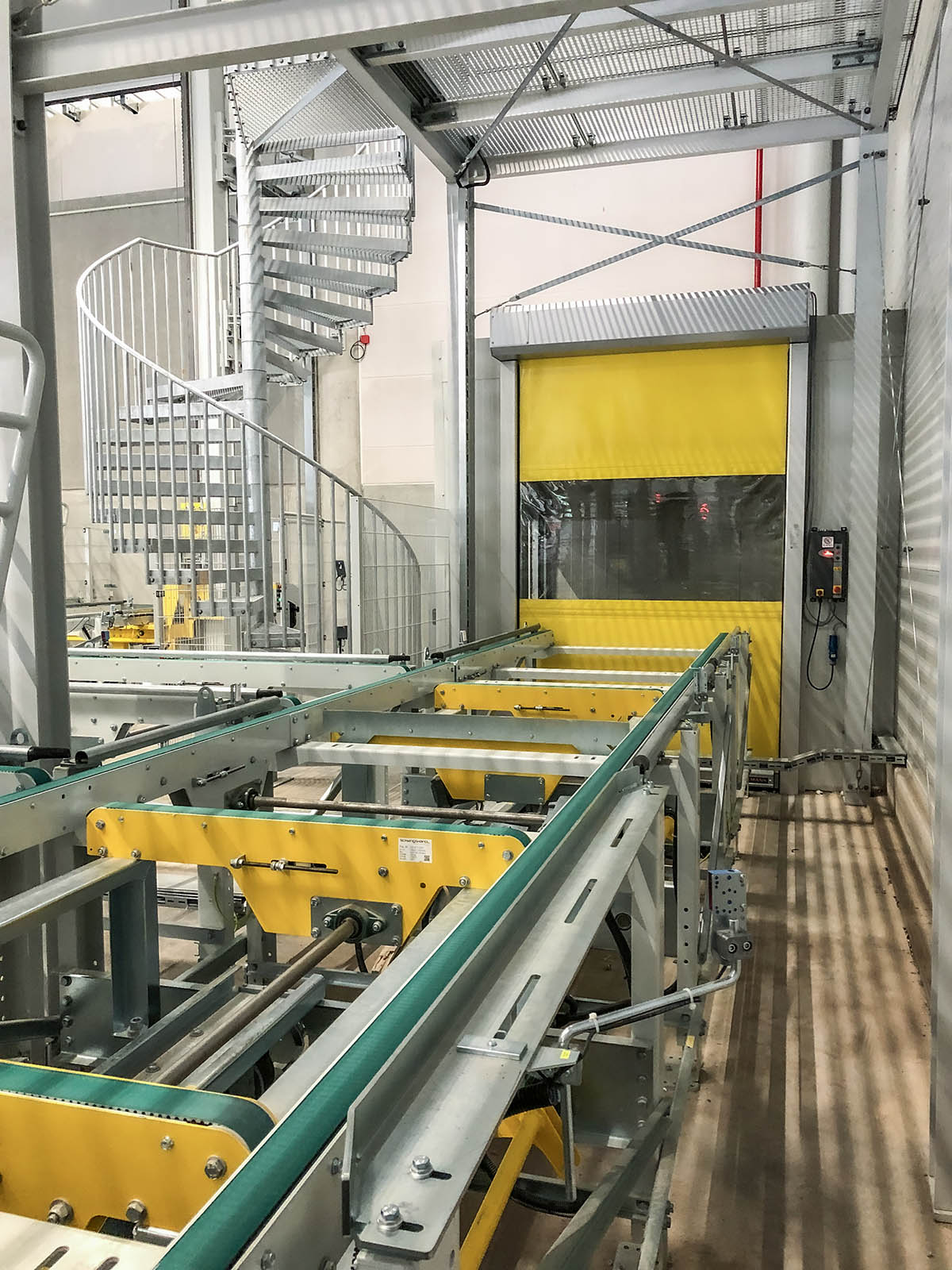
To ensure a smooth loading and unloading process into the trucks and to minimize physical exertion on the part of employees, UBH has implemented automatic loading of the bicycle cartons. A driverless transport system (DTS) removes the tray from the conveyor system and moves it to the dock leveller and from there on to the truck’s loading area. In the truck, the vehicle stops automatically depending on how full the truck is. Once the bicycle cartons have been removed manually, the empty tray returns to the conveyor system. Two driverless transport vehicles ensure a constant loading process, which avoids waiting times in the truck. When commercial goods are delivered - fully assembled bicycles from external production - the process differs only in that an empty tray is provided and a full one returns to the conveyor system. A total of four vehicles use envelope and laser navigation to find their way reliably.
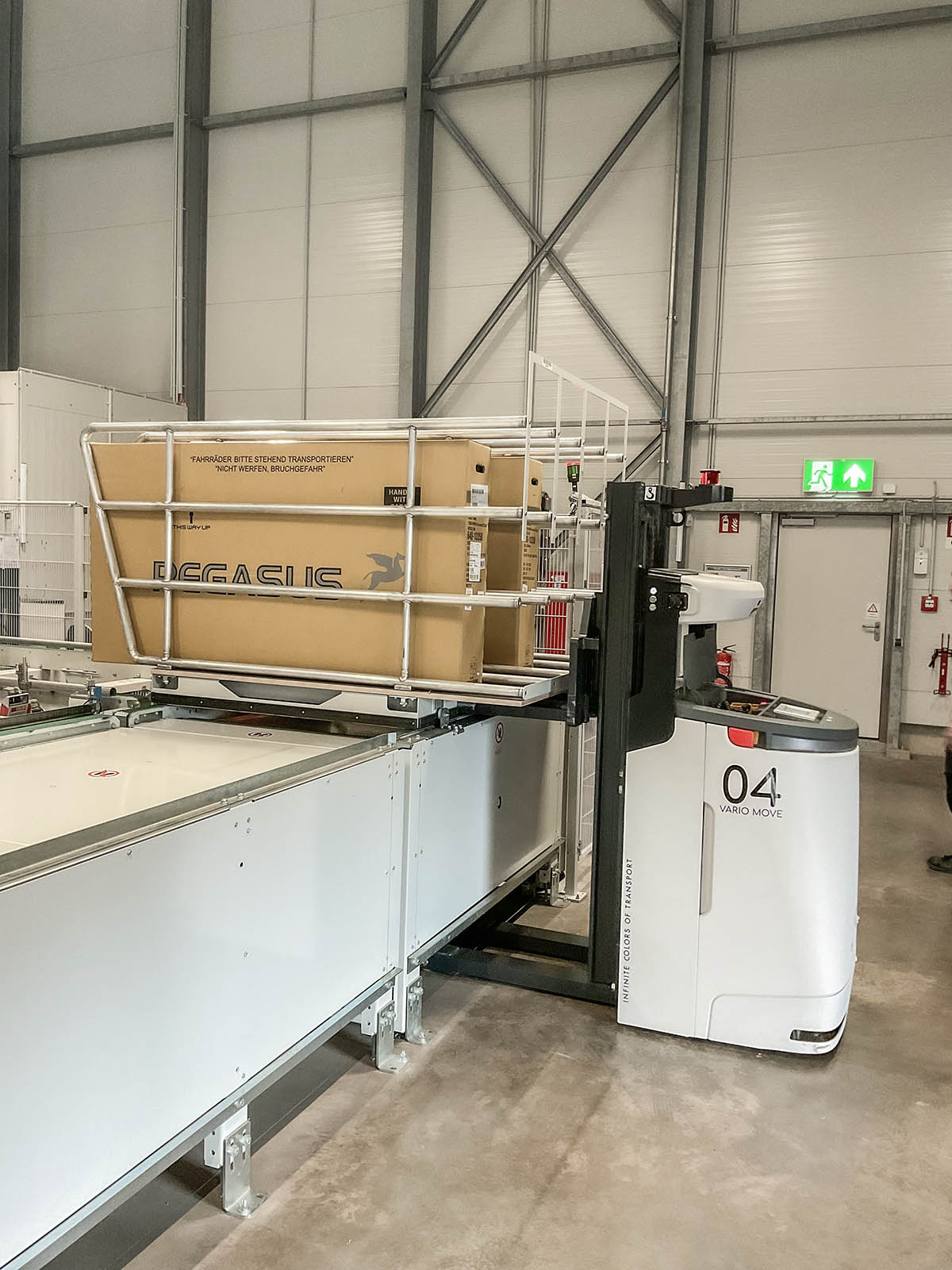
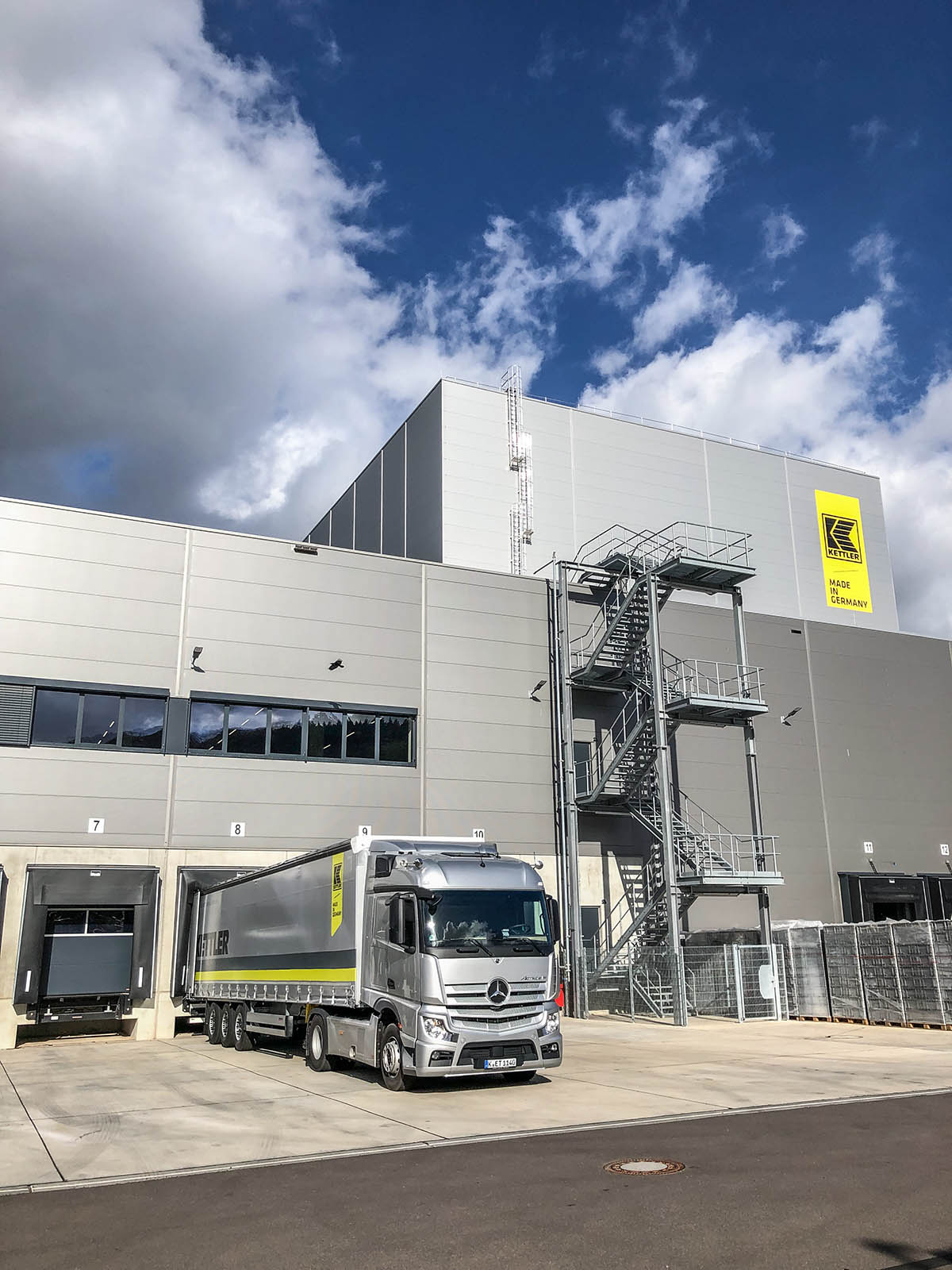
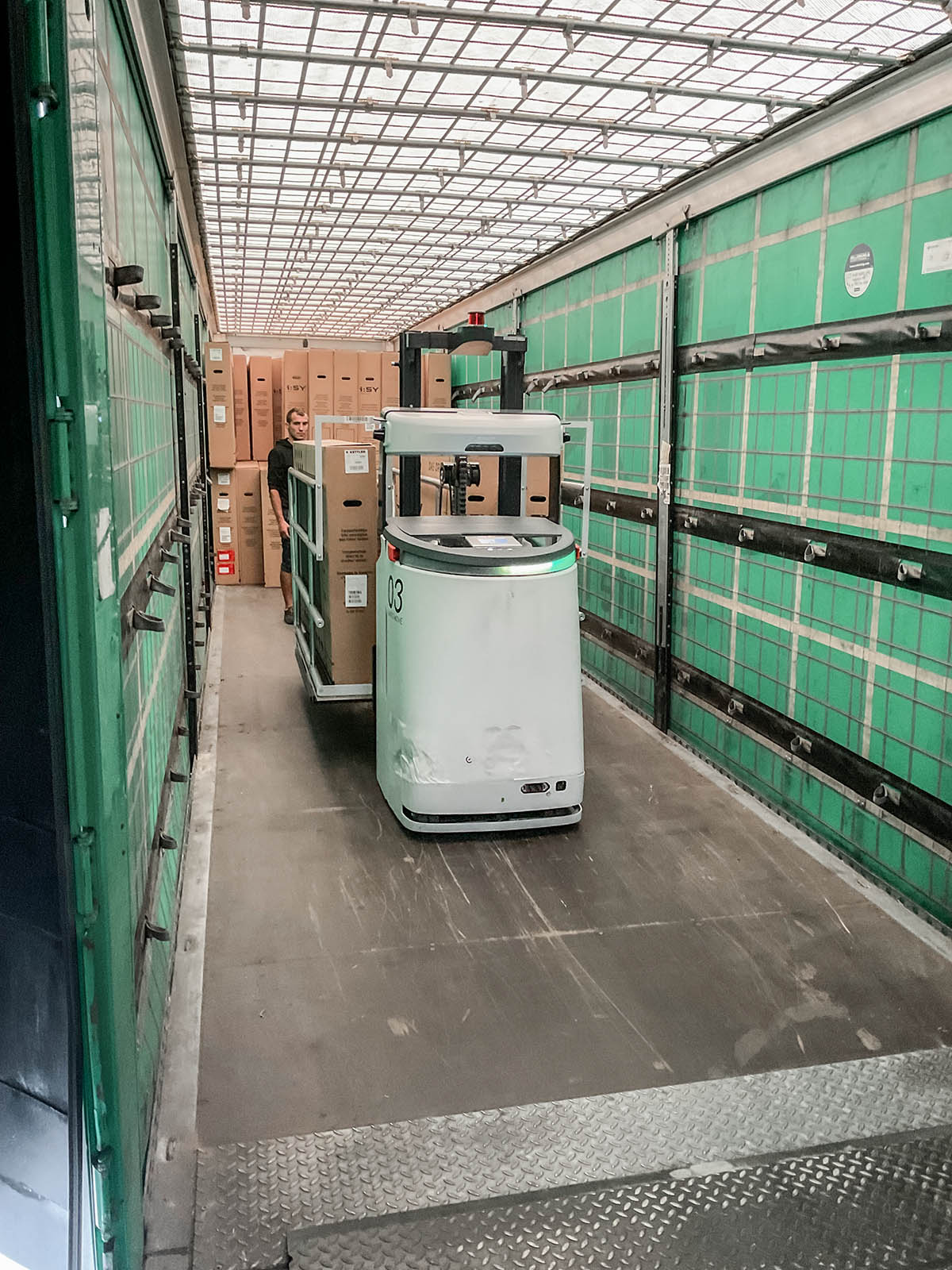
Reliable: Benchmark fire protection for safe processes
Fire safety is an important factor for maximum process reliability. The warehouse in St. Ingbert was therefore equipped with an individual fire protection solution consisting of active fire prevention in combination with early fire detection, which is considered a benchmark in terms of warehouse quality. Oxygen reduction comprehensively protects the stored e-bikes together with their lithium-ion batteries from the risk of fire. In a worst-case scenario/ If the worst comes to the worst, the oxygen content in the fully automated warehouse can be reduced to 13.6%, effectively containing fires or preventing them from starting in the first place.
The bicycle cartons are fed in and out via a conveyor loop that connects the pre-zone with the high-bay rack. Special air locks in the loop reduce the exchange of oxygen to a minimum at both transitions between the high-bay rack and the pre-zone. In addition, the silo-style high-bay warehouse has a sealed external façade. The computer-aided blower door measurement revealed an average n50 value of 0.03 air exchange rate per hour at negative and positive pressure.
Pioneering: state-of-the-art logistics made in Germany
KETTLER Alu-Rad's new bicycle plant in St. Ingbert is an impressive demonstration of how state-of-the-art intralogistics works today. UBH has made optimum use of the available space with intelligent process automation and sustainably enhanced efficiency. Innovative individual solutions in the context of a comprehensive state-of-the-art overall solution have created a flagship project that shows how innovative intralogistics can increase added value and thus keep Germany attractive as a production base. Automation at its finest for bicycles that move people can thus serve as a role model for many other industries.
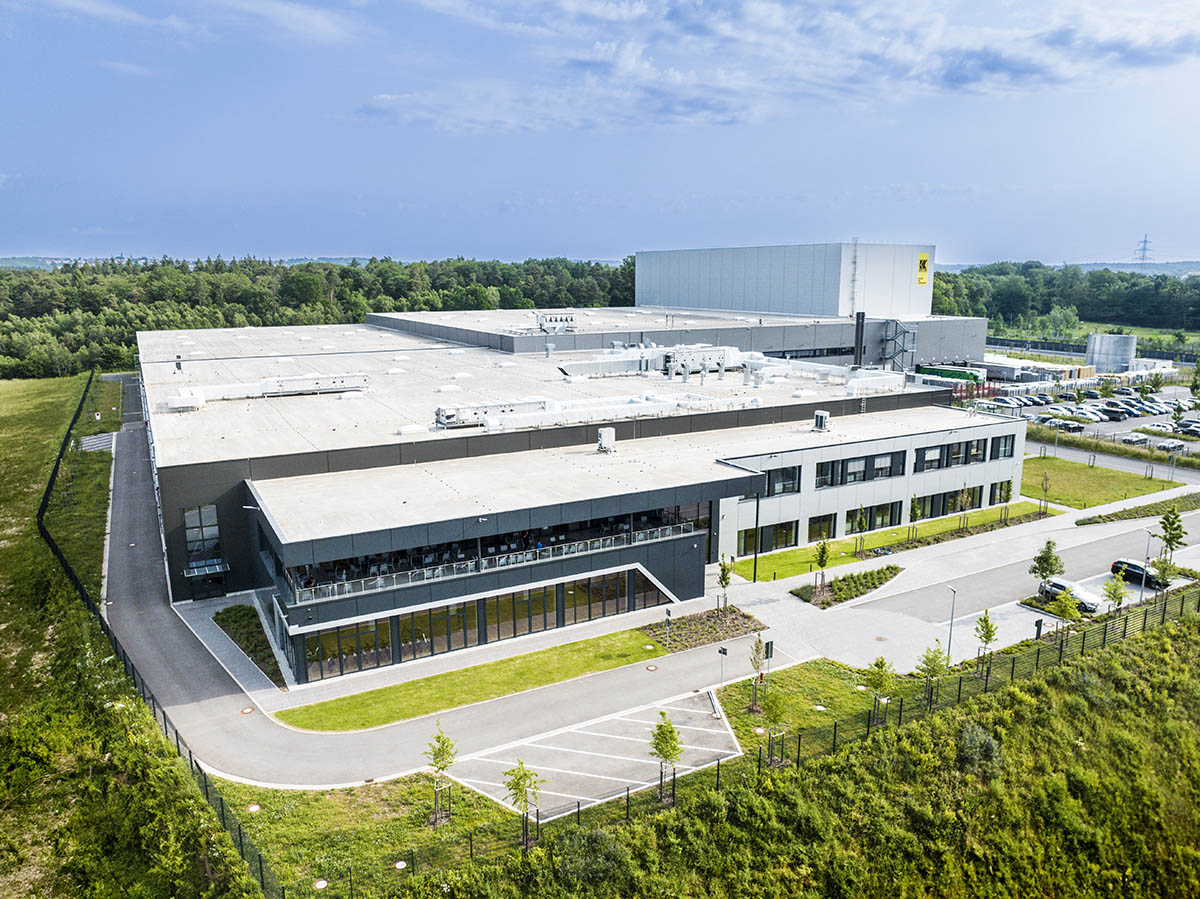
KETTLER Alu-Rad St. Ingbert
LogicsAI: KI-gesteuerter Materialflussrechner im Echteinsatz
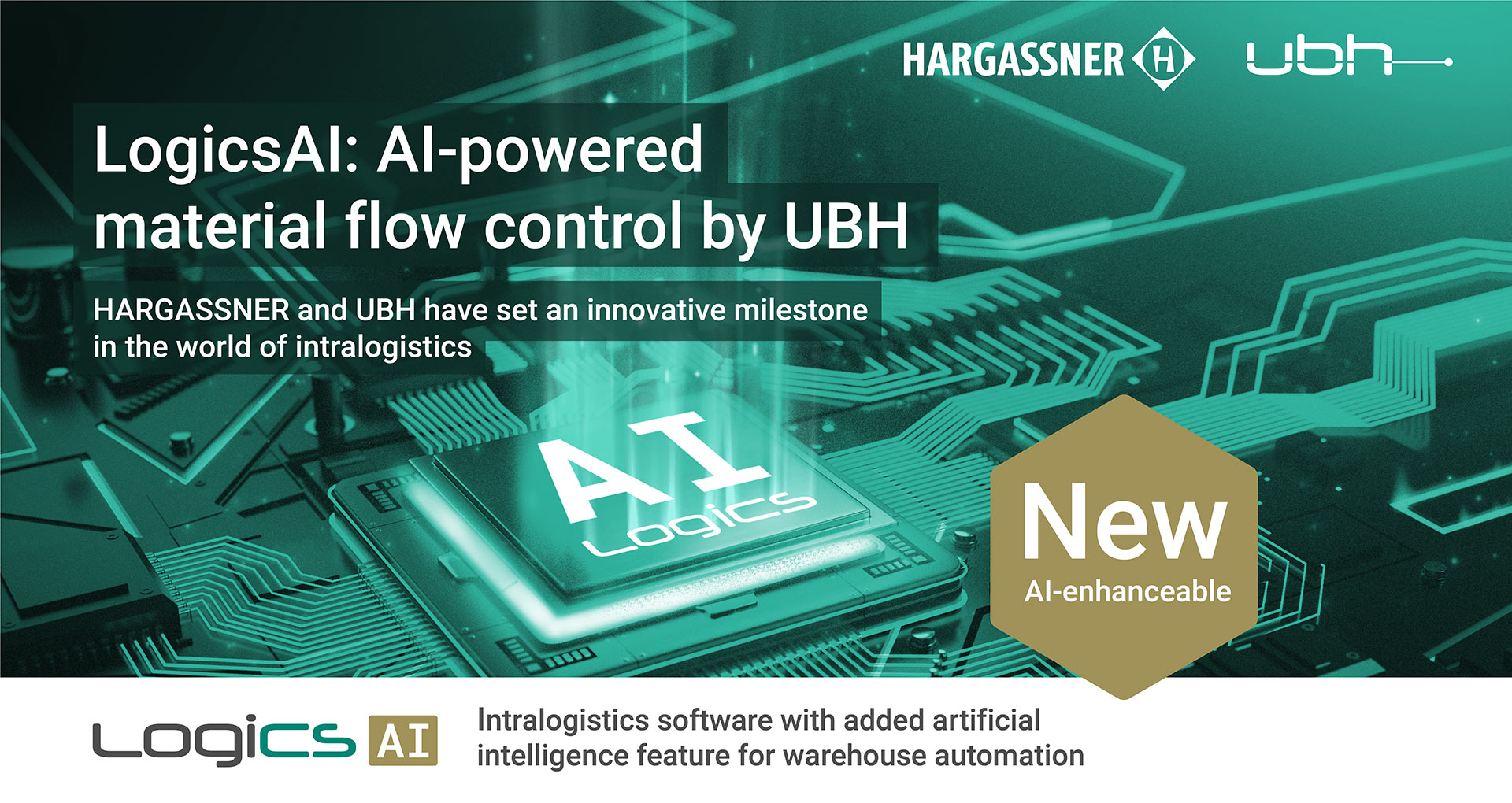
The cooperation between Austrian flagship enterprise HARGASSNER and UBH SOFTWARE & ENGINEERING based in Germany, represents a significant step towards Industry 4.0, namely operative deployment of artificial intelligence within in-plant transport via AI-powered material flow control. ‘Whilst hardware-related AI applications such as optimisation of robot motions or image processing have been in use for quite some time, we focussed on enhancing the system performance of existing conveyor systems by means of switching to an AI module on the existing MFC. The results exceed the values achieved by conventionally programmed material flow strategies by far. Even carefully crafted programming can never achieve the scenarios and dynamics of AI, which analyses and decides in real time,’ explains Gerald Gaberz, COO of UBH. `We are already working on extending our approach and envisage great potential for additional performance optimization of existing warehouse automation solutions. Thus, UBH can offer customers with existing systems an optimization that does not require costly extensions to machinery or building structures, i.e. a ‘retrofit plus, ’ so to speak.
M. Hargassner, owner: ‘We have always seen ourselves as an innovative company which provides its customers with intelligent, sustainable heating solutions – optimizing our internal logistics by deploying AI, thus creating an additional enhancement of our delivery capability, is simply a logical continuation of this philosophy!’
`The use of artificial intelligence to enhance efficiency within logistics is another step towards Industry 4.0.’, says Roland Neubauer, Industrial Engineer at HARGASSNER.
Commissioning of real operation is scheduled for the fourth quarter of this year.
Thumbnail Hargassner: HARGASSNER Ges mbH, with its headquarters in Weng i. I. (Upper Austria) and a workforce numbering 1,150, has been developing innovative heating systems for the past 40 years. The company is a frontrunner when it comes to biomass heating systems such as pellets, wood chips and log boilers, along with heat pumps and solar panels. Hargassner is synonymous with efficiency, reliability and consistent innovation when it comes to reducing energy consumption and emissions. The company now supplies sustainable heating solutions and renewable energies to 43 countries worldwide.