Newsroom
UBH auf der Common / POW3R 2024 – Zukunft mit IBM i gestalten!
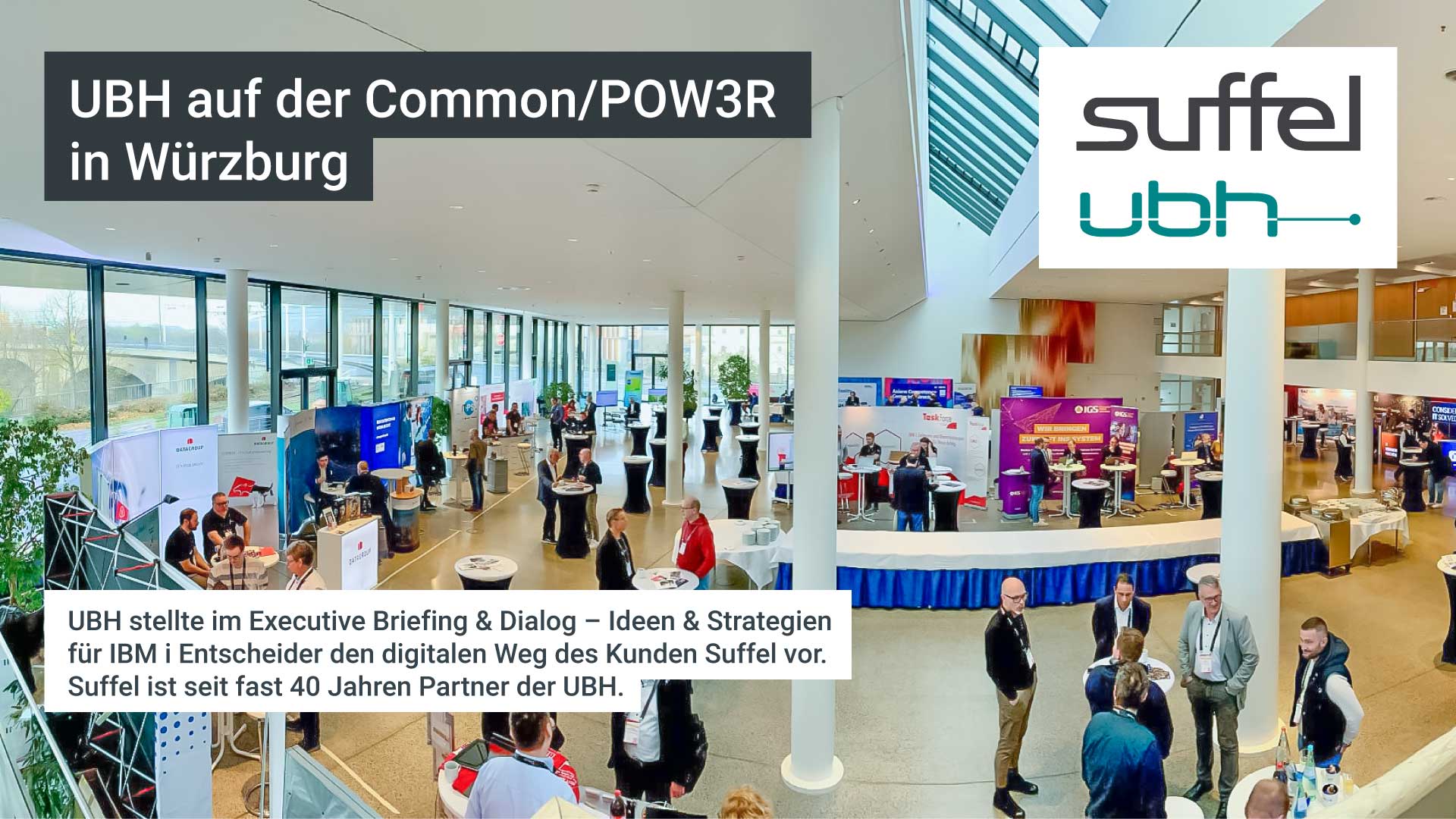
Die Zukunft mit IBM i – Erfolgreiche digitale Transformation mit UBH auf der Common / POW3R 2024
In der heutigen digitalen Welt ist eine zukunftsfähige IT-Infrastruktur der Schlüssel für den langfristigen Erfolg eines Unternehmens. Doch was bedeutet „zukunftsfähig“ im Kontext von IT? Und wie kann eine leistungsstarke Plattform wie IBM i Unternehmen dabei unterstützen, ihre Ziele zu erreichen? Diese Fragen standen im Mittelpunkt unseres Beitrags auf der Common / POW3R 2024 in Würzburg, wo wir gemeinsam mit unserem langjährigen Partner Suffel einen spannenden Einblick in den digitalen Transformationsprozess des Unternehmens gaben.
Ein Blick zurück und nach vorn: Suffels Reise in die digitale Zukunft
Bereits in den 80er Jahren begann die Reise von Suffel mit IBM i als Basisplattform für ihre ersten IT-Anwendungen. Seitdem hat sich das Unternehmen auch mit unserer Eigenentwicklung, dem ERP-System wEBV, kontinuierlich weiterentwickelt, um der steigenden Komplexität und den Anforderungen des Marktes gerecht zu werden. Heute zeigen Suffel und UBH, wie eine vollständig integrierte IT-Lösung alle Geschäftsprozesse eines Unternehmens abdeckt und optimiert.
Auf der Common / POW3R 2024 haben wir im Executive Briefing & Dialog gemeinsam mit Suffel den Weg hin zu einer modernen IT-Plattform präsentiert. Von den ersten, einfacheren Anwendungen in den 80er Jahren bis hin zur leistungsstarken, ganzheitlichen IT-Infrastruktur von heute – der digitale Weg des Unternehmens und unseres Systems wEBV ist ein perfektes Beispiel dafür, wie erfolgreiche Transformation aussehen kann.
Unsere maßgeschneiderte ERP-Lösung wEBV zeigt, wie ein vollintegriertes ERP-System mit leistungsstarken Add-Ons die spezifischen Anforderungen von Suffel komplett abdeckt. Sie ist flexibel und skalierbar, sodass sie mit dem Unternehmen wachsen kann – ein wichtiger Faktor für die digitale Zukunftsfähigkeit Ihres Unternehmens.
Was die Lösung von UBH und IBM Power so einzigartig macht, ist der hohe Grad an Digitalisierung – eine Entwicklung, die nicht nur die internen Prozesse optimiert, sondern auch die Kundenerfahrungen verbessert und so zum langfristigen Erfolg des Unternehmens beiträgt.
State of the Art mit wEBV & IBM Power: Die technologische Basis der Zukunft
Unsere Lösung wEBV setzt auf die bewährte IBM Power-Plattform, die als zentraler Dreh- und Angelpunkt für sämtliche Geschäftsprozesse fungiert. Mit der Integration moderner App-Anwendungen und einer benutzerfreundlichen Oberfläche haben wir eine Lösung geschaffen, die nicht nur effizient, sondern auch intuitiv zu bedienen ist.
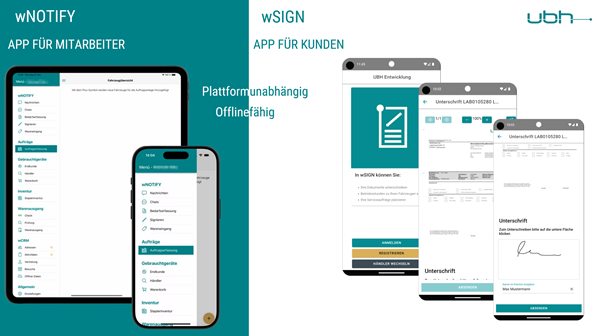
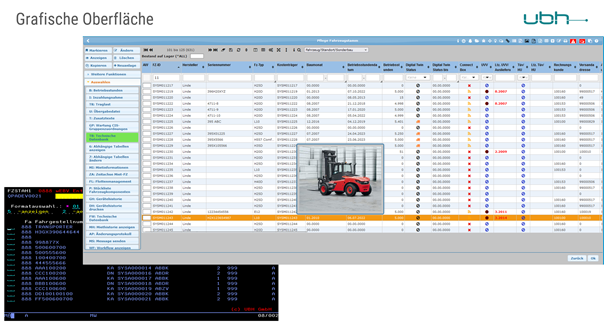
Software Oberflächen
Warum eine moderne IT-Plattform so wichtig ist
Der digitale Wandel ist kein kurzfristiger Trend, sondern eine langfristige Notwendigkeit. In Zeiten von Big Data, Cloud-Computing und Künstlicher Intelligenz benötigen Unternehmen eine IT-Infrastruktur, die flexibel, sicher und leistungsfähig ist. wEBV bietet genau diese Vorteile und ermöglicht es Unternehmen, schnell auf Marktveränderungen zu reagieren und gleichzeitig die Kontrolle über ihre Daten und Anwendungen zu behalten.
Für uns ist klar: Digitalisierung ist der Schlüssel zum Erfolg. Doch die wahre Herausforderung besteht nicht nur darin, die richtigen Technologien zu implementieren, sondern auch, eine Plattform zu schaffen, die sich über Jahre hinweg weiterentwickeln lässt.
Was denken Sie? Welche Rolle spielt eine moderne IT-Plattform für den langfristigen Erfolg eines Unternehmens?
Wir sind gespannt auf den Austausch an Erfahrungen und Meinungen mit Ihnen! Welche Herausforderungen haben Sie bei der Digitalisierung in Ihrem Unternehmen erlebt? Welche Technologien halten Sie für zukunftssicher? Teilen Sie Ihre Gedanken mit uns in den Kommentaren!
Mehr erfahren und in Kontakt treten
Wenn Sie mehr über die Lösungen von UBH und unsere Erfahrungen mit der IBM Power-Plattform erfahren möchten, kontaktieren Sie uns direkt! Wir freuen uns darauf, Ihnen zu zeigen, wie auch Ihr Unternehmen von einer modernen, flexiblen und skalierbaren IT-Infrastruktur profitieren kann.
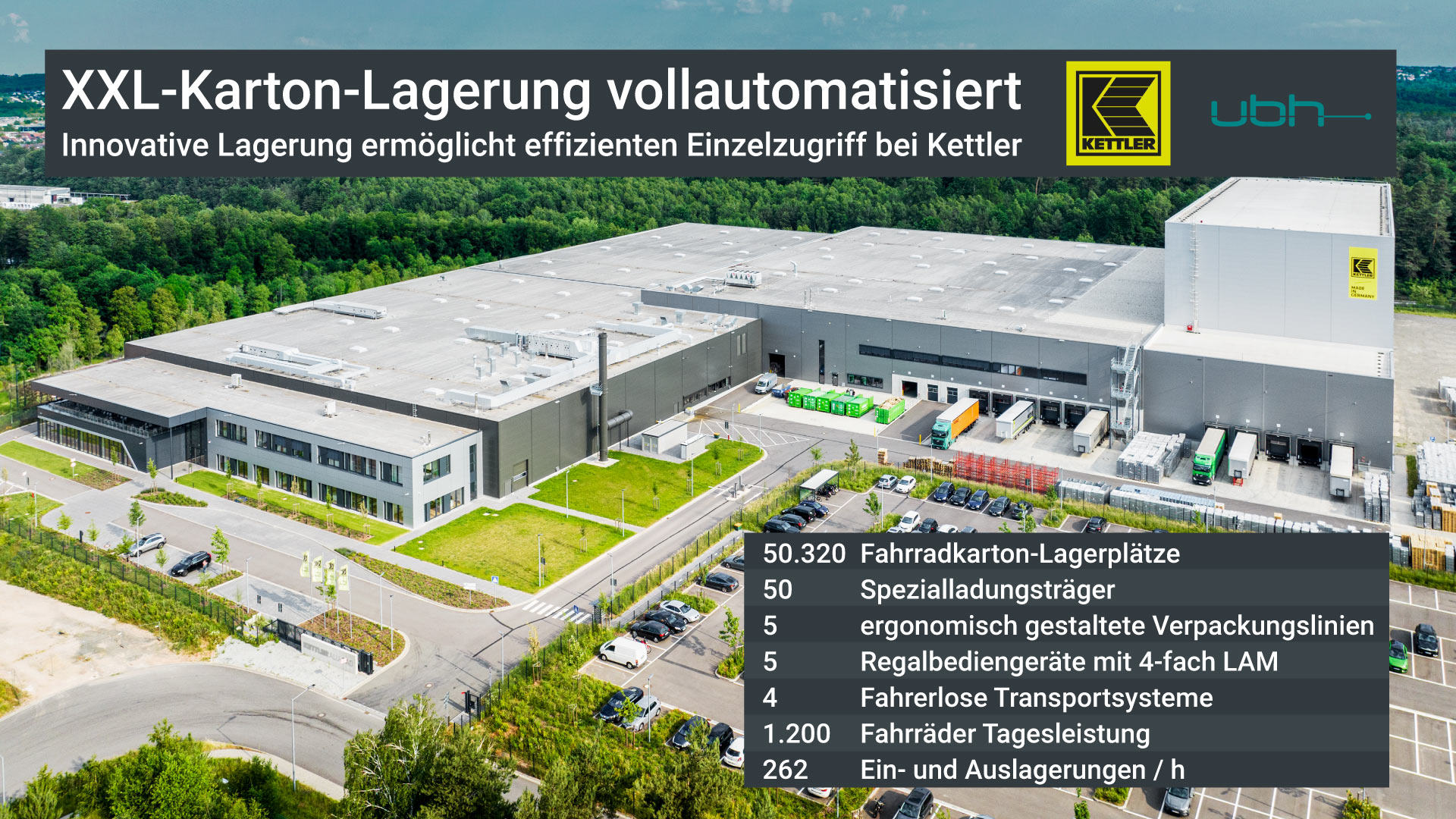
100 Millionen Euro Investitionssumme, 62.000 Quadratmeter Fläche, 300 Arbeitsplätze – das 2022 Fahrradwerk von KETTLER Alu-Rad im saarländischen St. Ingbert ist ein Bekenntnis zum Standort Deutschland. Damit sich die E-Bike-Montage Made in Germany auch lohnt, hat UBH SOFTWARE & ENGINEERING GmbH die Effizienz der Intralogistik auf ein neues Niveau gehoben.
Niveau bedeutet in St. Ingbert nicht nur fertigungstechnische Klasse. Im Werk von KETTLER Alu-Rad steht Niveau auch für wegweisende Intralogistiklösungen, die den Raum auf mehreren Ebenen in eine hoch effiziente dreidimensionale Prozessstruktur verwandeln. Eine wegweisende Rolle kommt dabei dem Handling von UBH zu, das interne logistische Prozesse vollautomatisiert – von der Verpackung und dem Transport über Lagerung und Kommissionierung bis hin zur Verladung der Fahrradkartons. Immerhin müssen an dem zu den modernsten und größten Fahrradwerken Europas zählenden Standort täglich bis zu 1.200 Fahrräder schnell und sicher bewegt werden. Gelungen ist dies durch ein intelligentes Zusammenspiel von IT und lückenlosen mechanischen Warenflüssen. Dazu hat UBH als Generalunternehmen die gesamte Informations- und Steuerungstechnik, die Spezialfördertechnik, das fahrerlose Transportsystem, die Regalbediengeräte und das Hochregallager mit Vorzonengebäude in Silobauweise geplant, entwickelt und implementiert.
Herausforderung: High-Mix-Low-Volume stellt Automatisierung auf die Probe
Im KETTLER Alu-Rad-Werk St. Ingbert ist Prozesssicherheit ein zentraler Bestandteil der intralogistischen Fertigwaren-Abläufe. Erfordert auch die Montage der E-Bikes noch Handarbeit, so erfolgen Verpackung, interner Transport, Ein- und Auslagerung, Kommissionierung und Versand vollautomatisch. Zu Beginn der Montageprozesse verlassen die zukünftigen Bikes ihr eigentliches Terrain und gehen in die Luft. In einem an der Decke installierten Rahmenfördersystem von vier Kilometern Länge aufgehängt, findet der Rahmen seinen Weg vollautomatisch durch das gesamte Werk – von der Lackiererei bis zu den vier Montagelinien mit einer Kapazität von über 600 E-Bikes am Tag im Einschichtbetrieb. Unmittelbar im Anschluss an jede Montagelinie erfolgen Verpackung und automatischer Abtransport.
Eine hohe Flexibilität der Automatisierung erfordert das High-Mix-Low- Volume-Produktspektrum von KETTLER Alu-Rad mit unterschiedliche Kartongrößen. Gelöst hat UBH die Anforderung innovativ mit einer Eigenentwicklung, die auf Bodenniveau jeden einzelnen Fahrradkarton vertikal transportiert, im IT-System erfasst, vereinnahmt, umreift und verschließt.
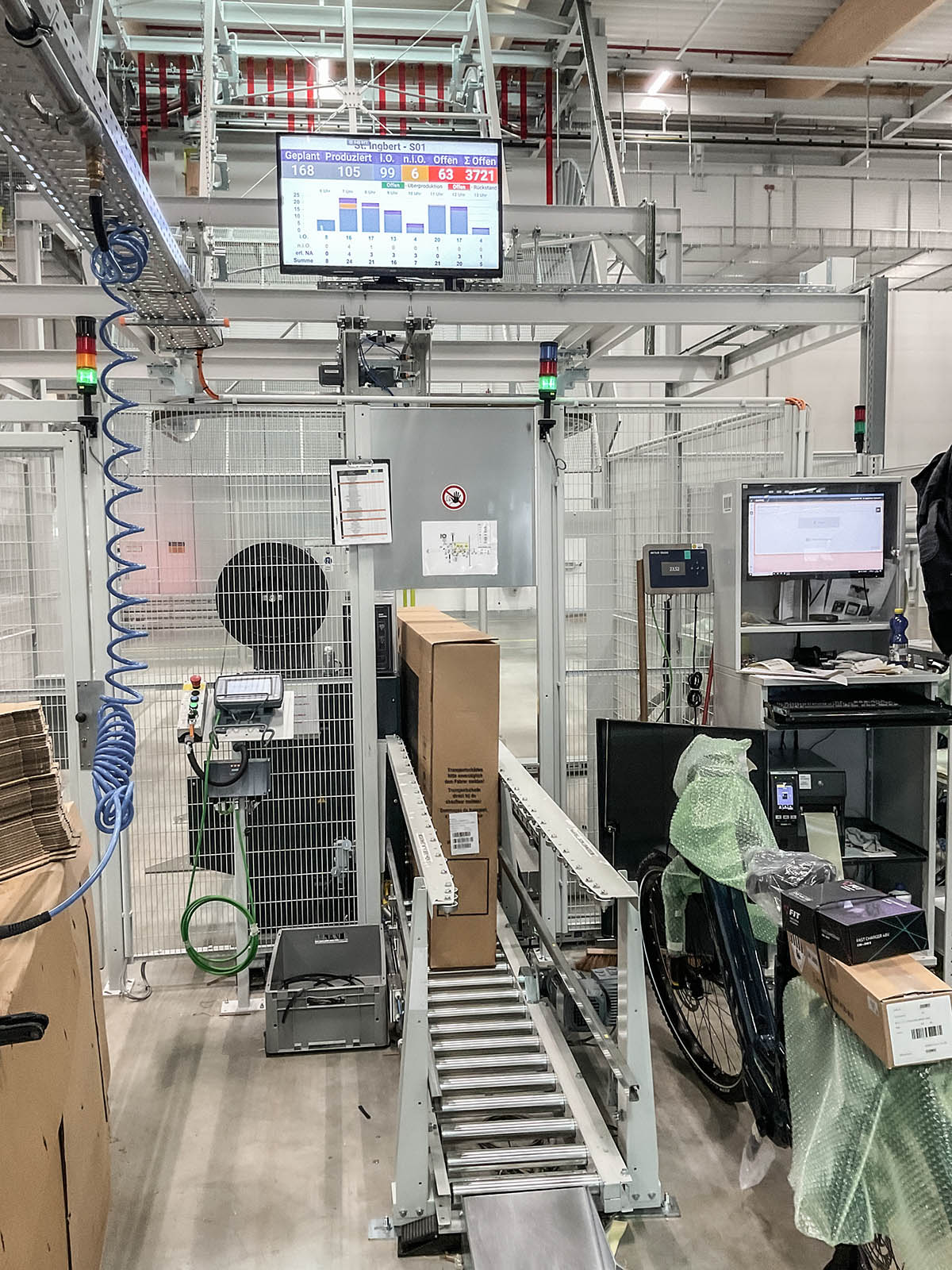
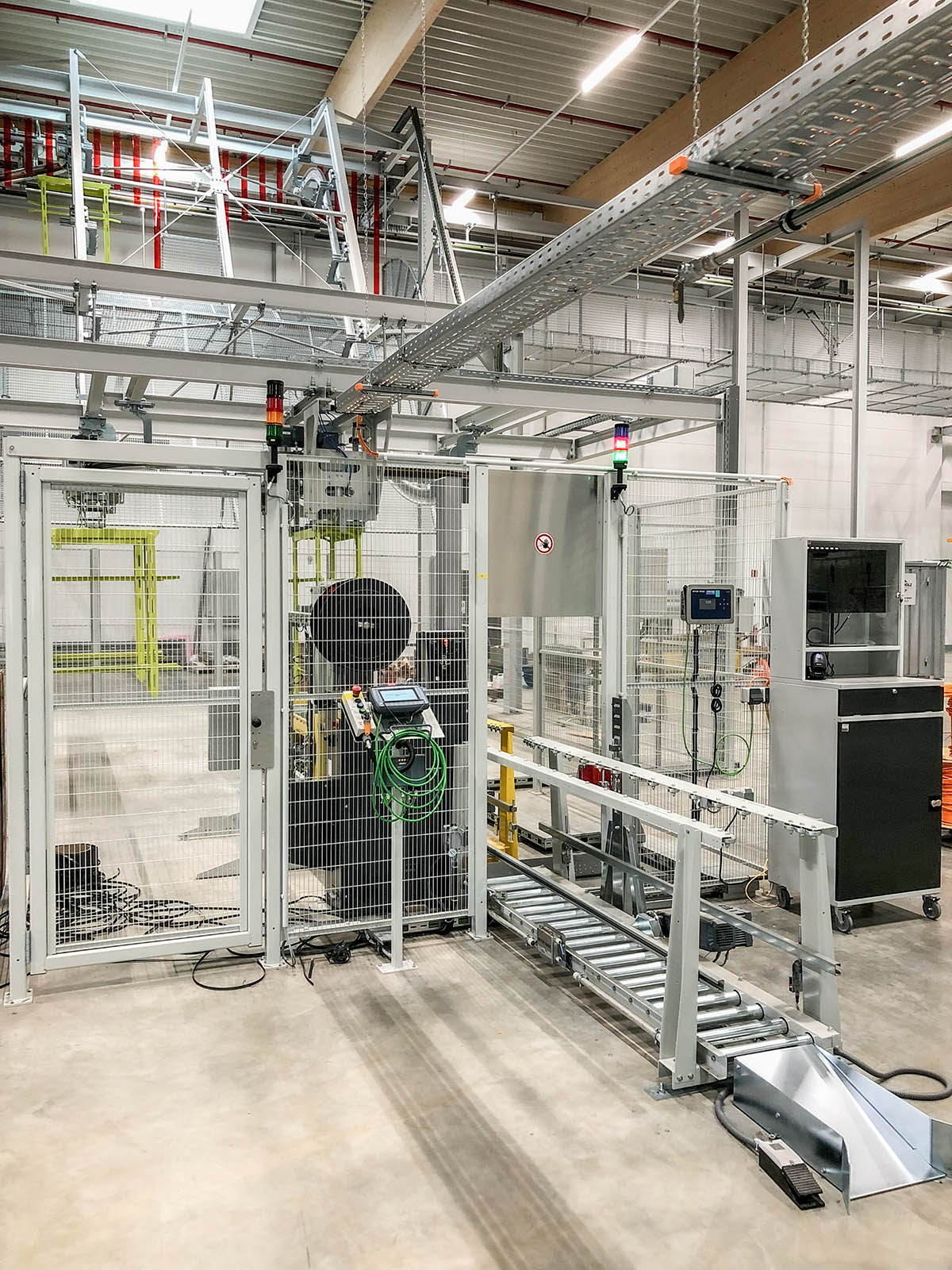
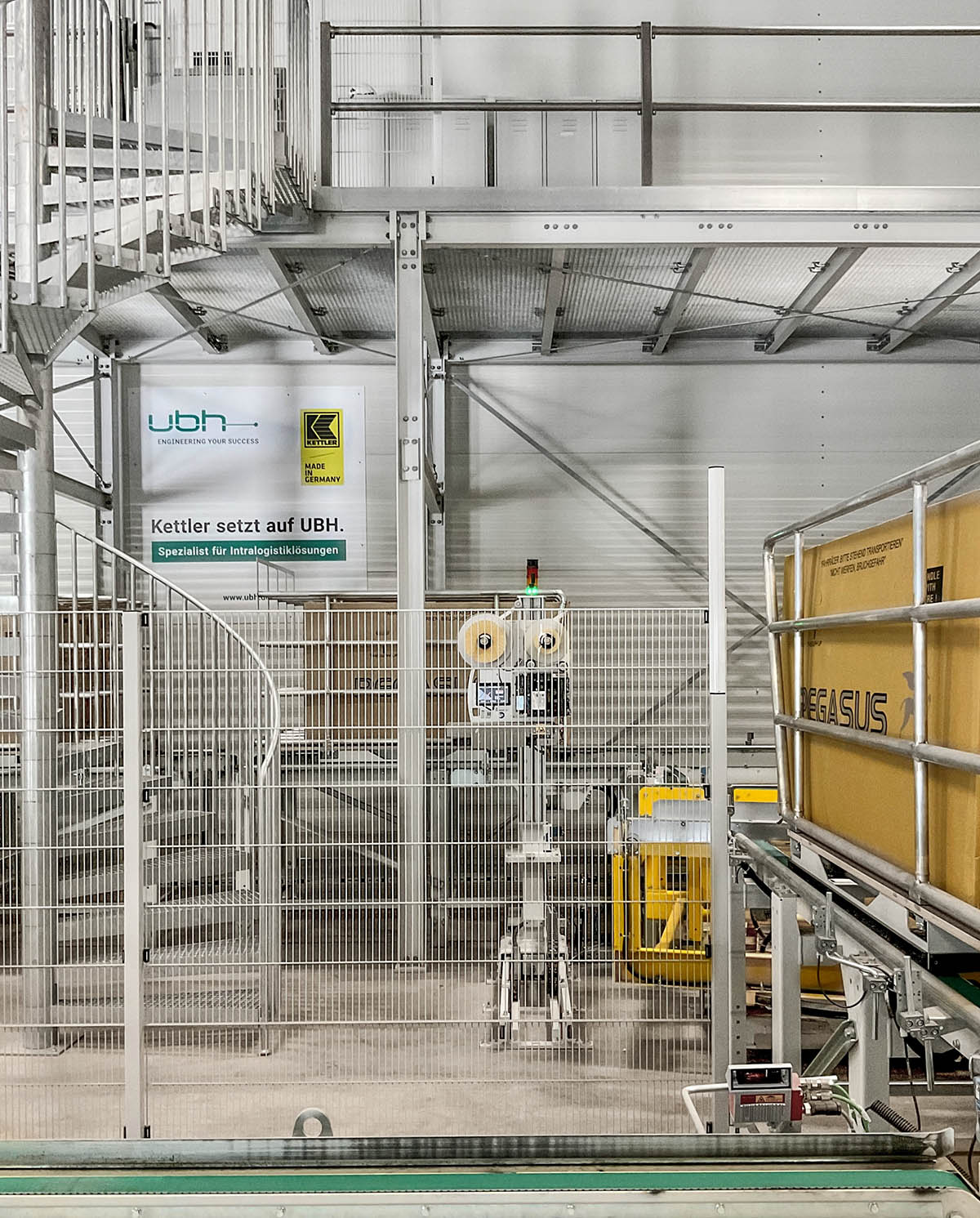
Verpackungslinie
Eine mögliche Kapazitätserweiterung für eine 5te Montagelinie ist vorbereitet. Alle fünf Förderstrecken sind reversierbar und ermöglichen einen automatischen Abtransport sowie eine automatische Zuführung der Fahrradkartons an die Linien. Davon profitieren neben KETTLER Alu-Rad auch andere Marken, die zur Zweirad-Einkaufs-Genossenschaft (ZEG) gehören. In St. Ingbert werden neben Kettler auch Premium-Segmente von BULLS, ROTWILD, Hercules, Zemo und i:SY montiert.
Wertschöpfung: Bike-Transport in großer Höhe macht den Shopfloor frei.
Am Ende der 7,5 m langen Auf- und Abgabelinien übergibt die Bodenfördertechnik die Fahrradkartons an eine Elektrohängebahn und bringt sie auf ein Transportniveau unter der Hallendecke von neun Metern Höhe. Da jede der fünf Linien über eine eigene Übergabestation verfügt, lassen sich Transportaufträge unabhängig voneinander fahren. Der Transport unter der Decke bot bereits für die Werksplanung einen großen Vorteil: ein freier Shopfloor für gesteigerte Wertschöpfung. Hindernisse wie fertige Fahrräder und mögliche Beschädigungen werden vermieden, wie sie sonst durch Flurförderfahrzeuge beim Abtransport verpackter Bikes entstehen können. Das zeigt sich heute noch in einem einwandfreien Erscheinungsbild, wie Michael D`Erme, Werksleiter KETTLER Alu-Rad, bestätigt: „Nach zwei Jahren Produktionsbetrieb sieht das Werk immer noch aus wie neu.“ Für eine Stundenleistung von 150 Einzelfahrten verfügt die Elektrohängebahn über 20 Gondeln. Dem Streckenverlauf der Elektrohängebahn sind fünf Produktionslinien auf Bodenniveau, eine Wartungsbucht und ein Zwischengeschoss, Mezzanine genannt, auf 6,5 m Höhe angeschlossen. Alle drei Bereiche stellen eigene Brandabschnitte dar und wurden mit speziellen Brandschutztoren ausgestatten, durch die die Gondeln fahren.
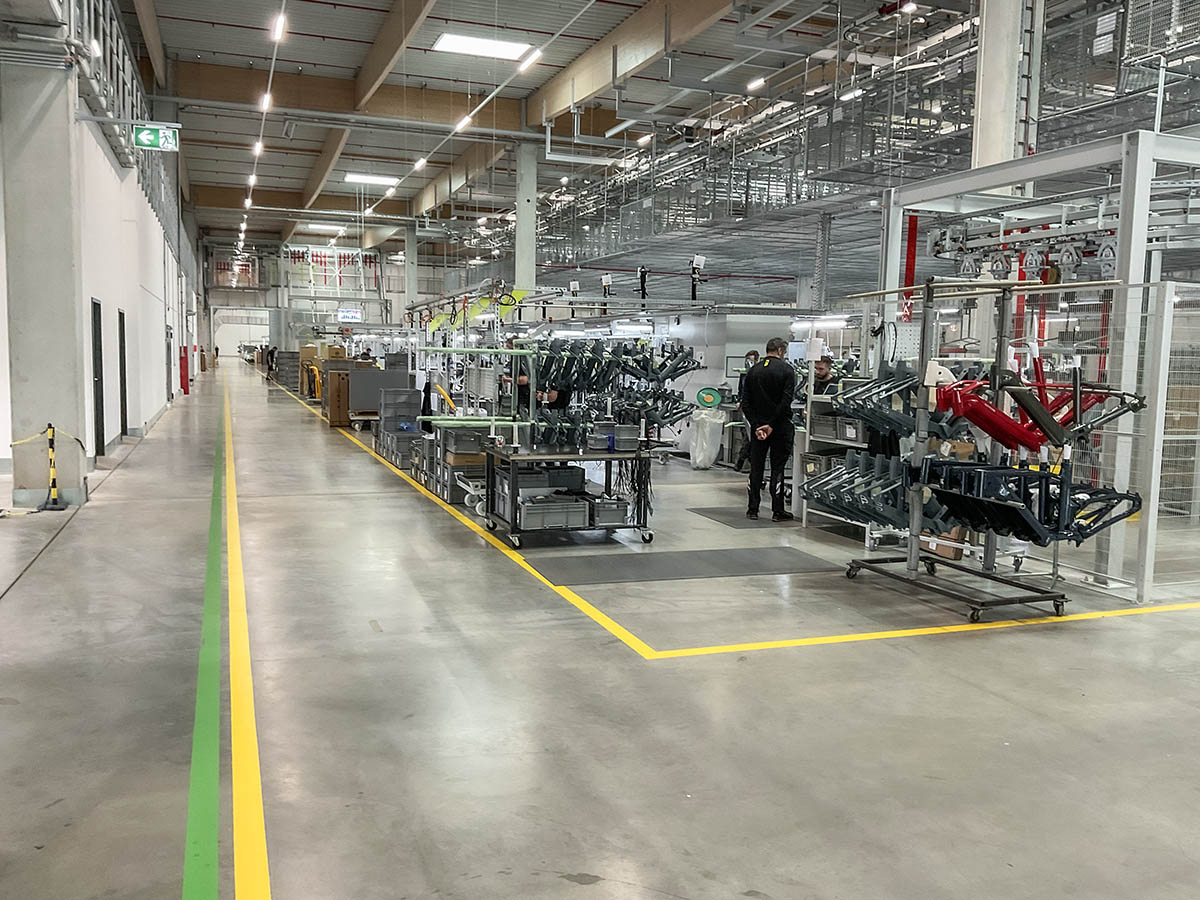
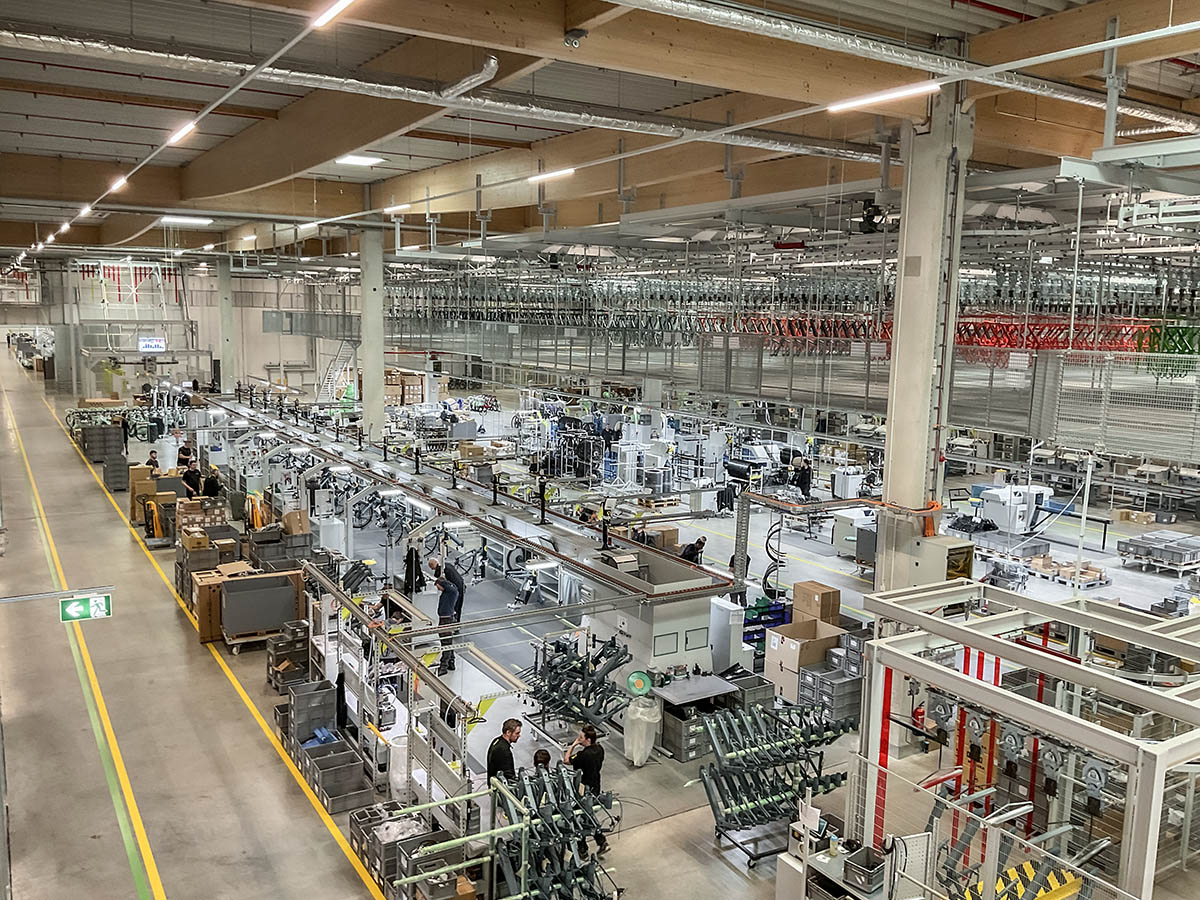
Shopfloor und Produktionslinie
Leistungsverdichtung: Entkoppelte Prozesse für effizienten Materialfluss
Die Mezzanine verbindet über eine Strecke von 100 m die Produktion mit der Vorzone zum Hochregallager. Unmittelbar darunter befinden sich auf Bodenniveau der Wareneingang und das Rohwarenlager. Zwei Riemenförderbahnen transportieren auf eigens dafür entwickelten Trays jeweils vier Fahrradkartons. Daraus resultiert eine Leistungsverdichtung auf der Förderstrecke sowohl in der Zuführung als auch im Abtransport. Die Übergabe der Fahrradkartons vom Hängeförderer auf Vierfach-Trays und zurück erfolgt automatisch. Um Prozesse zu entkoppeln und einen hoch effizienten Materialfluss zwischen Produktion, Verbindungsstrecke, Vorzone und Hochregallager zu ermöglichen, lassen sich auf der Mezzanine jeweils bis zu 20 Trays mit 80 Fahrrädern auf der Zuführstrecke und der Abführstrecke zwischenpuffern. Der Handshake zwischen Mezzanine und Vorzone erfolgt über zwei Vertikalförderer, die die Trays auf Riemenfördertechnik übergeben. Da es sich um zwei Brandabschnitte handelt, wurde an dieser Stelle ein weiteres Brandschutztor verbaut.
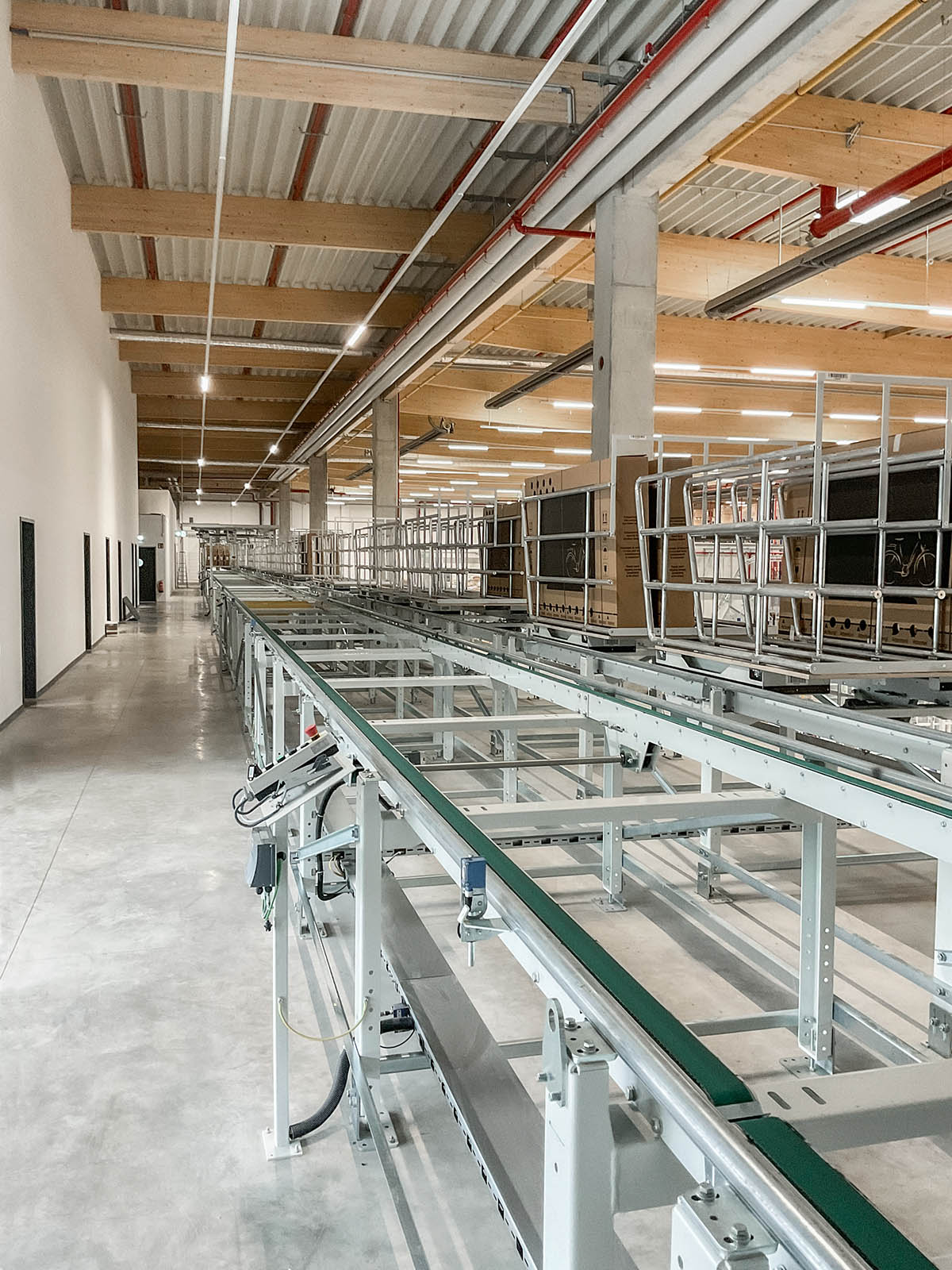
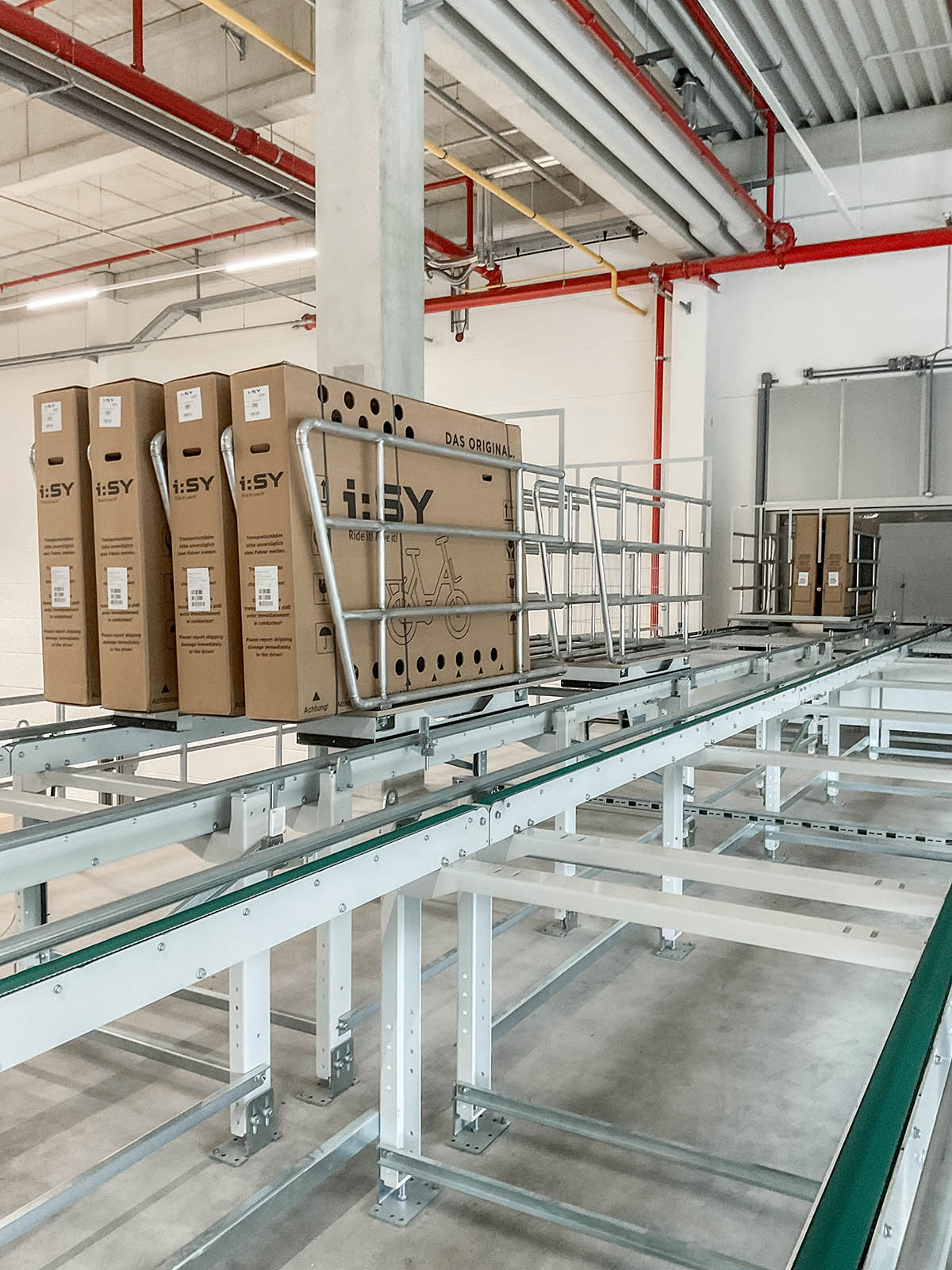
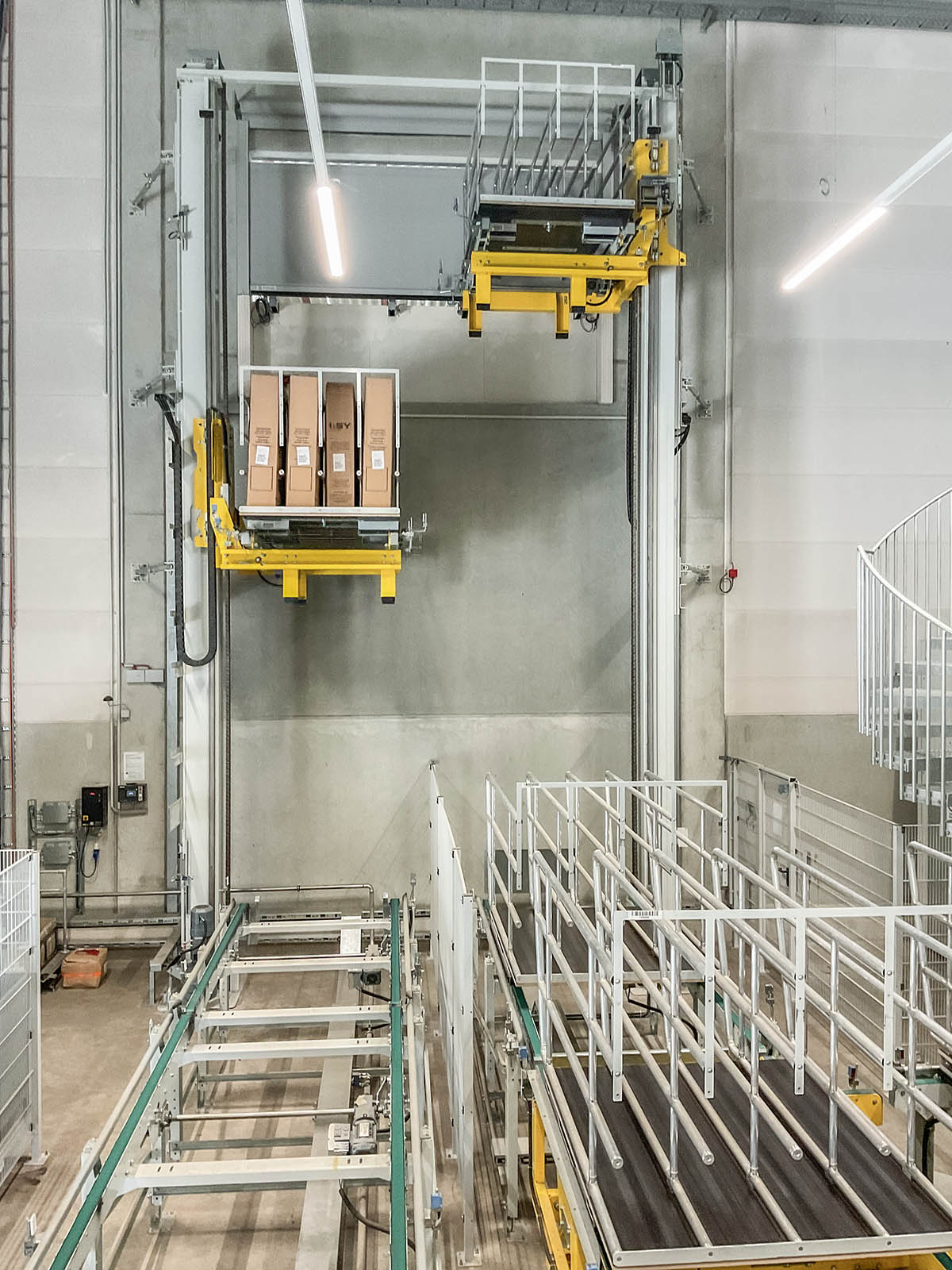
Fördertechnik auf Mezzanine
Superlativ: 50.320 E-Bikes im Hochregallager mit 107.000 m3
Das Hochregallager und die Vorzone wurden in Silobauweise errichtet und zählten zum Lieferumfang der UBH. Die Vorzone mit den Abmessungen von 35 m Breite, 18 m Tiefe und 14 m Höhe bildet das logistische Zentrum, in dem alle Materialflüsse der Fertigware mit einer Tagesleistung von 1.200 Fahrrädern zusammenkommen. Warenströme aus Produktion, Hochregallager und von den Andocktoren bewegen sich zeitgleich inbound und outbound und verlaufen damit parallel in beide Richtungen. Dies vermeidet ein Bottleneck. Fünf Andocktore in der Giebelwand öffnen sich zum angrenzendem Tiefhof für LKWs. Auf einer Fläche von 630 m2 entstand eine voll automatische Vorzone mit Zugang über eine Bühne für Personal und Besucher zu Wartungsbereichen und Hochregallager. Die Abmessungen der in 4,5 m Höhe montierten Bühne betragen 29 m Breite und 3 m Tiefe.
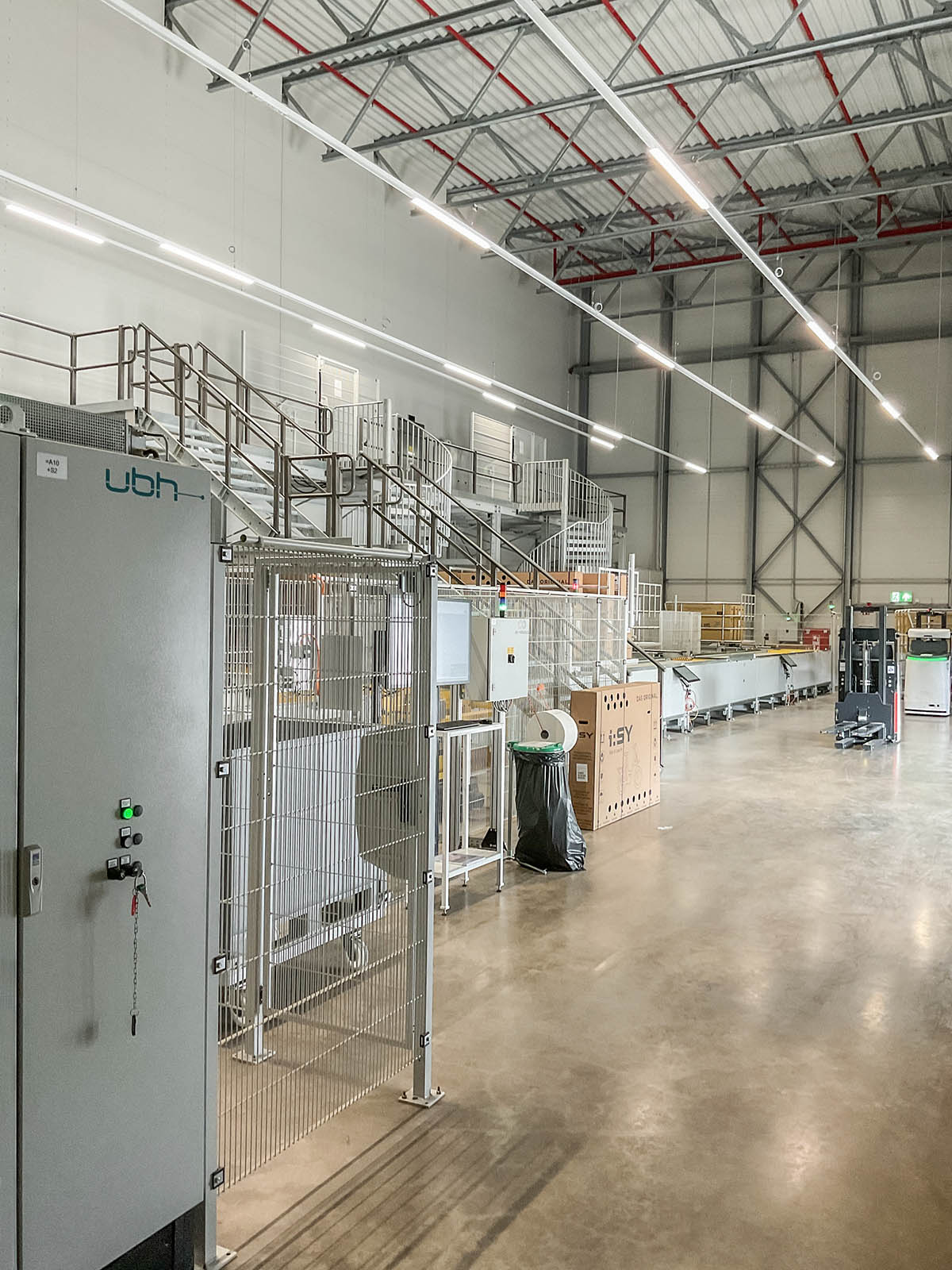

Bühne
Ein echter Superlativ stellt auch das hermetisch abgeriegelte Hochregallager dar. Bis unter die Decke bietet es Raum für 50.320 E-Bikes im Einzelzugriff. Insgesamt besitzt das Lager ein Volumen von 107.000 m3 bei 31 m Gassenhöhe und 96 m Gassenlänge. Auf fünf Regalgassen verteilt sich das eigens für KETTLER Alu-Rad entwickelte Regalsystem, das jeden Fahrradkarton ohne Tray einzeln lagern kann. Den Transport im Hochregallager übernehmen fünf Regalbediengeräte mit einer Ein- und Auslagerleistung von über 260 Kartons die Stunde. Doch das ist noch lange nicht alles. Das Hochregallager kann weit mehr als Fahrradkartons ein- und auslagern. Ein weiteres Highlight ist die vollautomatische Kommissionierung. Hierzu verfügt jedes Regalbediengerät über ein eigens entwickeltes vierfach Lastaufnahmemittel. Durch die Einführung der neuen Technologie ist KETTLER Alu-Rad in der Lage, Fahrradkartons voll automatisch zu kommissionieren und bei der Ausführung der Kundenbestellungen eine Null-Fehler-Garantie abgeben zu können.
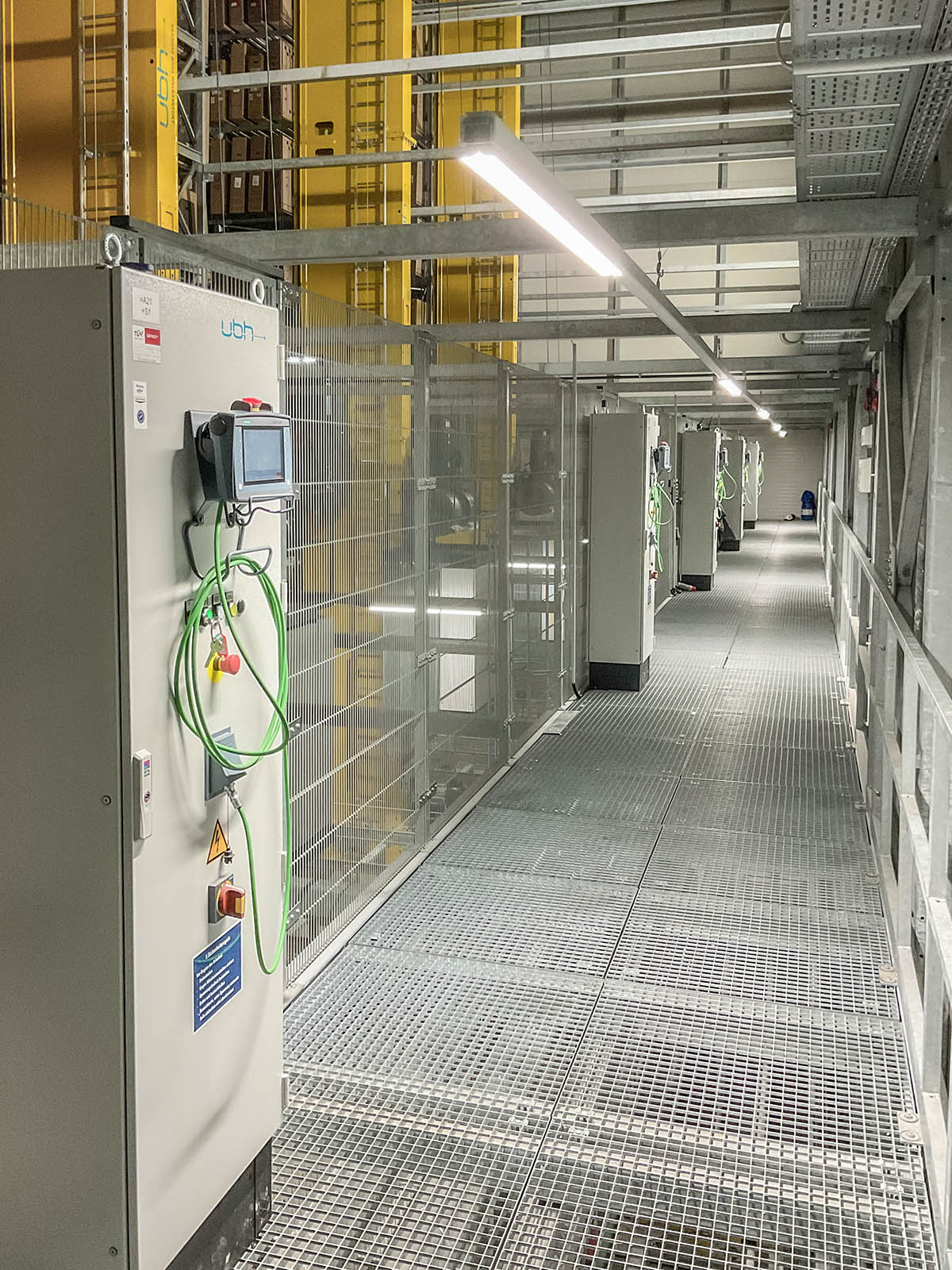
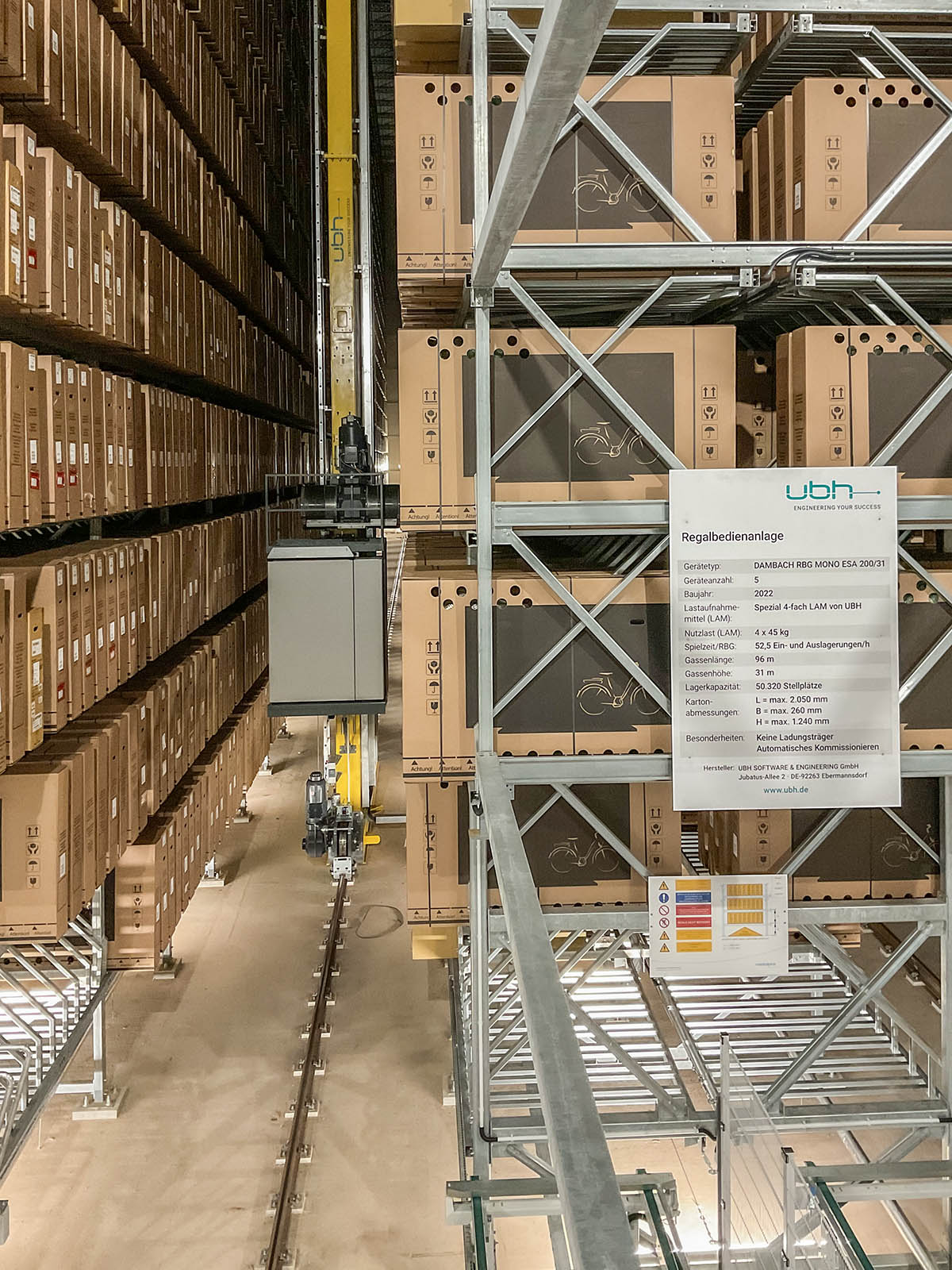
Hochregallager mit Regalbediengerät
Lückenlos: Vollautomatische Intralogistik bis in den LKW
Im Anschluss an die automatische Kommissionierung übergibt das Vierfach-Lastaufnahmemittel die Fahrradkartons auf leere Trays, die über den Materialflussrechner (MFC) LogiCS von UBH gesteuert werden und am Fördertechnikloop just-in-time bereitstehen. Die insgesamt zwei Ein- und Auslagerplätze für Trays im neuen Distributionszentrum bei KETTLER Alu-Rad sind an das Netzwerk von Regalbediengeräten und Fördertechnik angebunden. Vor Verladung in den LKW etikettieren zwei automatische Stationen die Fahrradkartons mit Versandlabel.
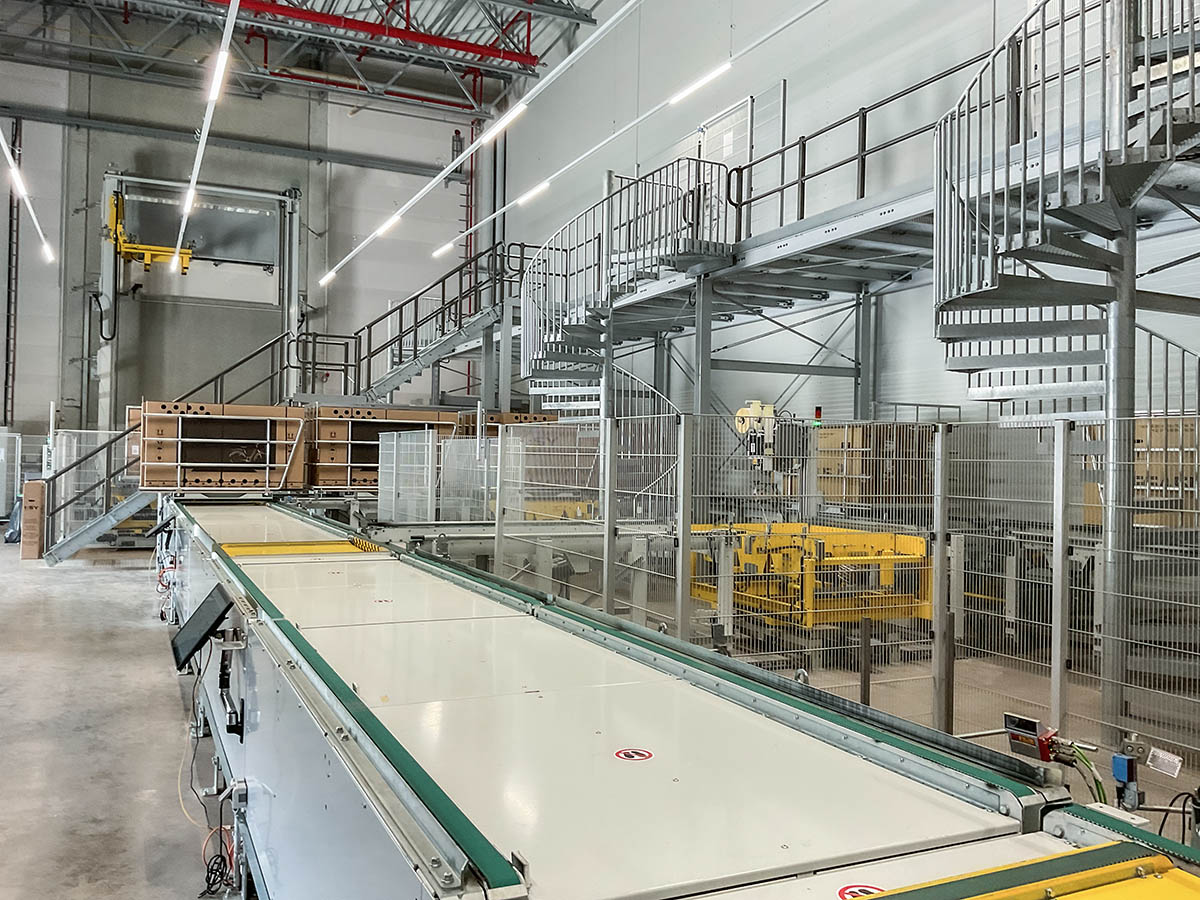
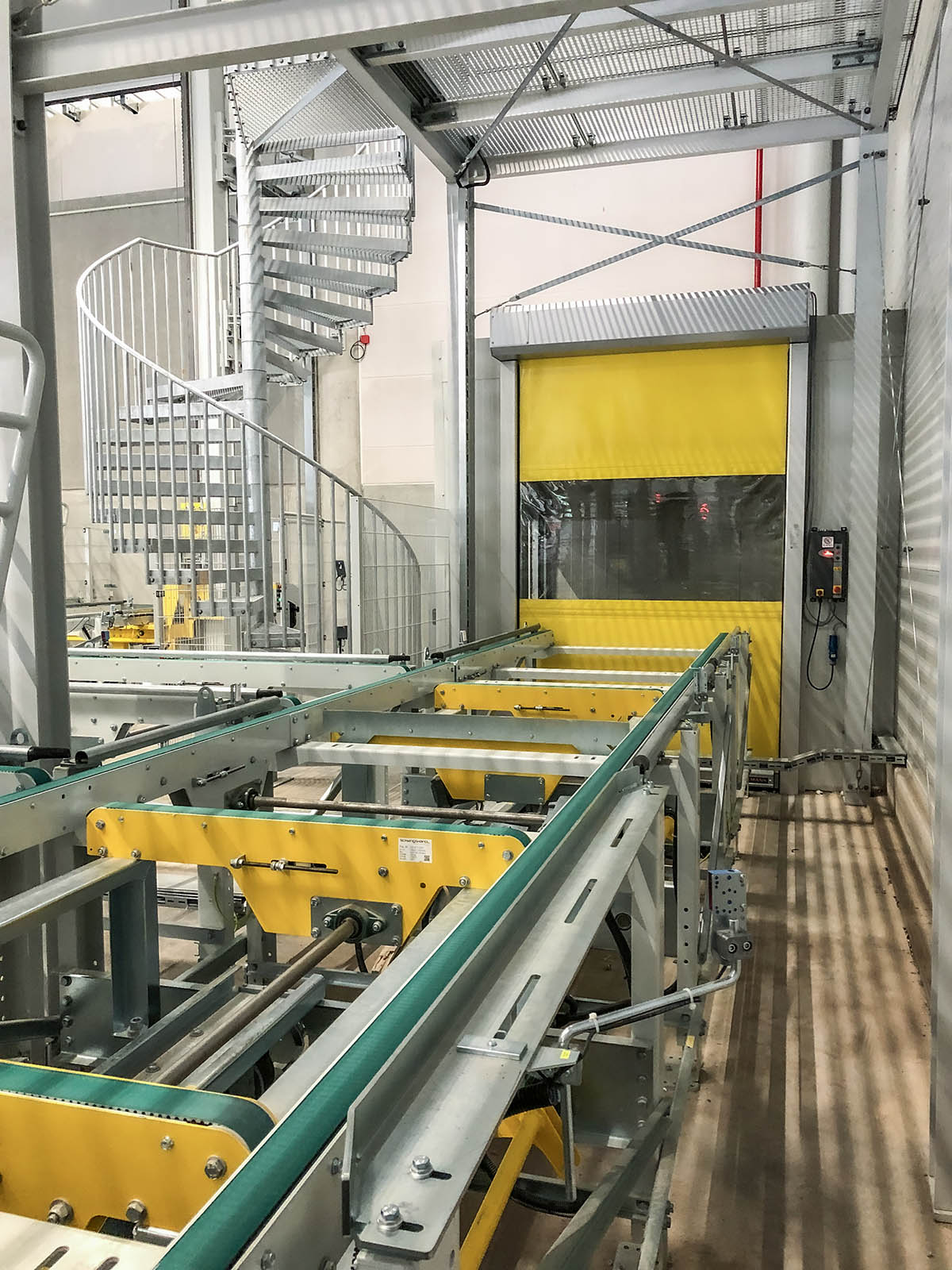
Vorzonengebäude mit Fördertechnik
Zum Sicherstellen eines reibungslosen Lade- und Entladeprozesses in die LKWs und um die körperlichen Anforderungen für Mitarbeitende zu minimieren, hat UBH eine automatische Verladung der Fahrradkartons realisiert. Dabei nimmt ein fahrerloses Transportsystem (FTS) den Tray von der Fördertechnik ab und fährt damit zur Überladebrücke und weiter auf die LKW-Ladefläche. Im LKW stoppt das Fahrzeug automatisch je nach Füllgrad. Nachdem die Fahrradkartons manuell entnommen wurden fährt das leere Tray zurück auf die Fördertechnik. Für einen konstanten Verladeprozess sorgen zwei FTS, was Wartezeiten im LKW vermeidet. Bei Anlieferung von Handelsware – vollständig montierte Fahrräder aus externer Produktion – unterscheidet sich der Prozess lediglich dahingehend, dass ein leerer Tray bereitgestellt wird und ein Voller auf die Fördertechnik zurückfährt. Insgesamt finden vier Fahrzeuge über Hüllkurven und Lasernavigation zielsicher ihren Weg.
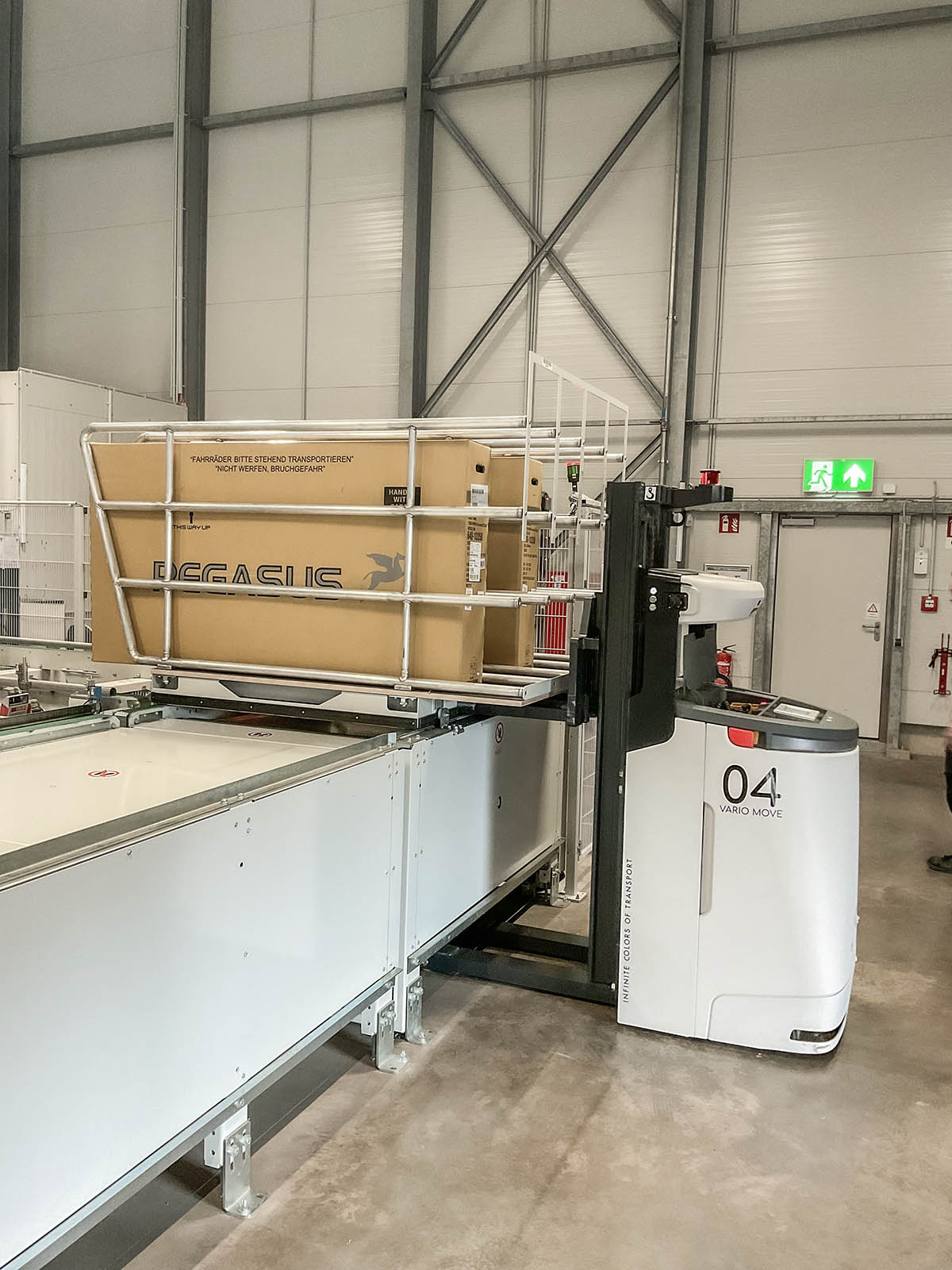
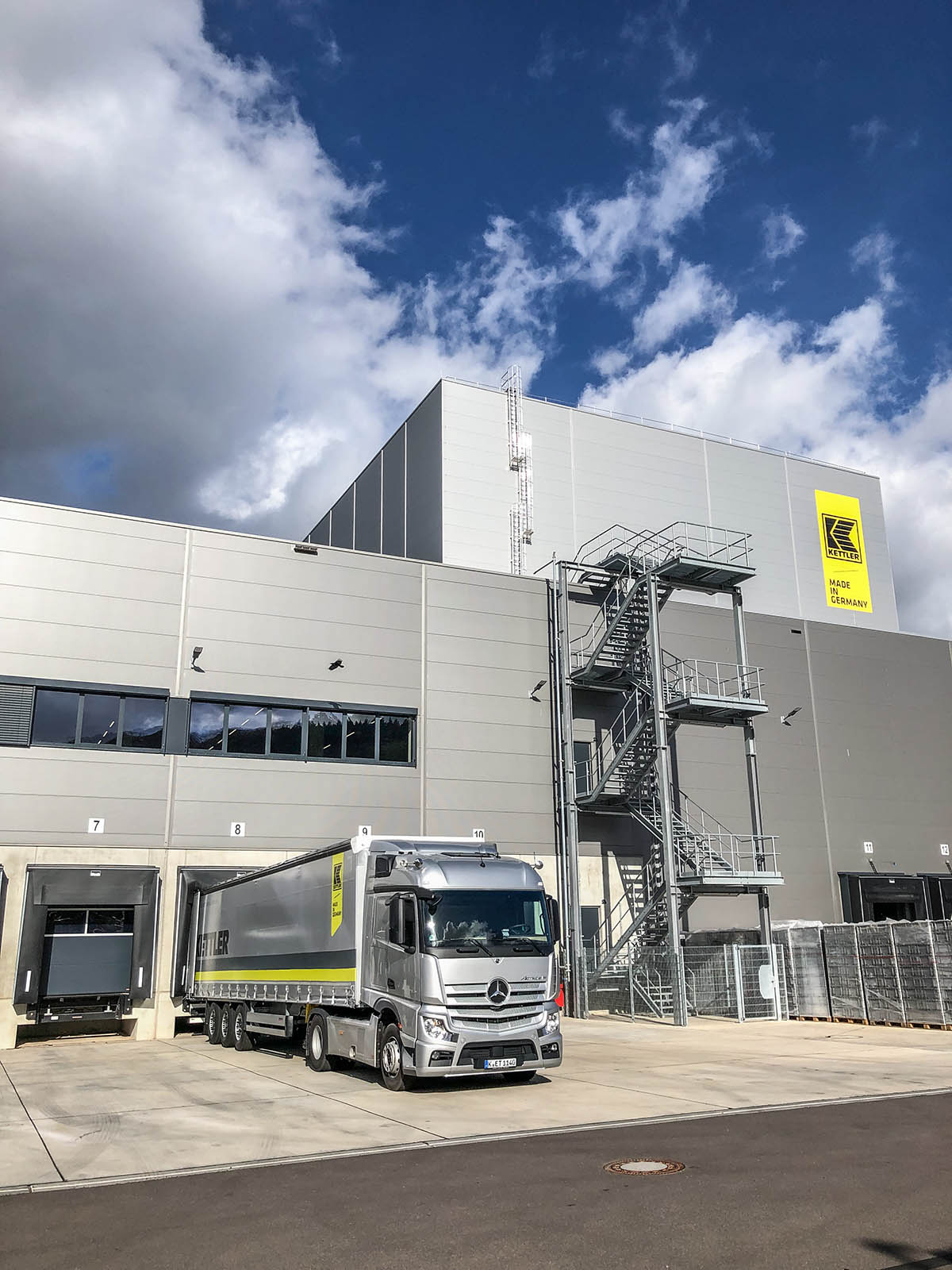
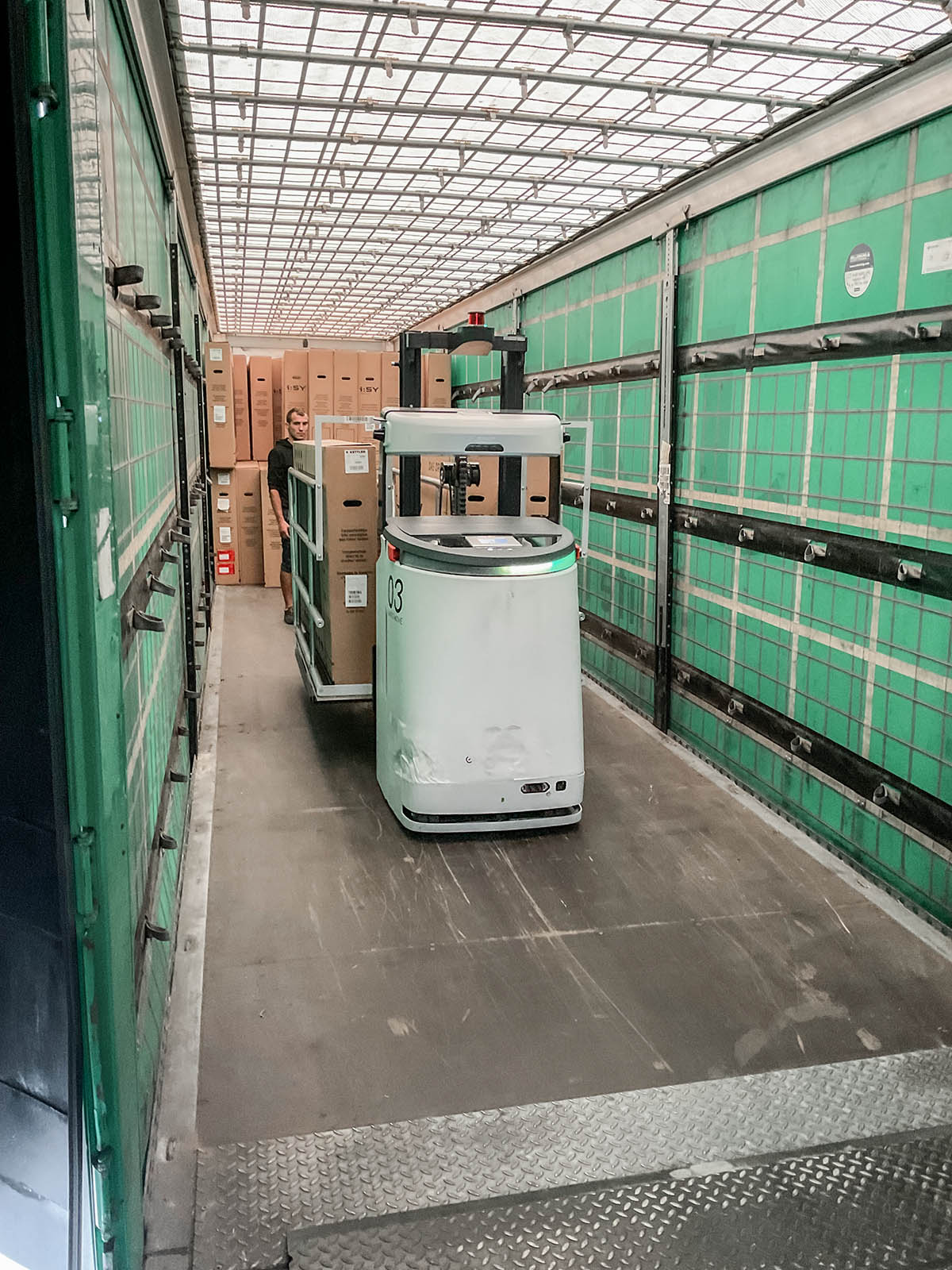
Zuverlässig: Benchmark-Brandschutz für sichere Prozesse
Ein wichtiger Faktor für maximale Prozesssicherheit ist die Brandsicherheit. Das Lager in St. Ingbert wurde dafür mit einer Individuellen Brandschutzlösung aus aktiver Brandvermeidung in Kombination mit Brandfrüherkennung ausgestattet, die als Benchmark in Sachen Lagerqualität gilt. Eine Sauerstoffreduzierung schützt die eingelagerten E-Bikes mitsamt Lithium-Ionen-Akkus umfassend vor Brandgefahren. Hierfür kann im Fall der Fälle der Sauerstoffgehalt im voll automatisierten Lager auf 13,6 % heruntergefahren werden. Dies dämmt Brände wirkungsvoll ein oder lässt sie erst gar nicht entstehen. Die Zu- und Abführung der Fahrradkartons erfolgt über einen Fördertechnikloop, der die Vorzone mit dem Hochregal verbindet. Spezielle Luftschleusen im Loop verringern bei beiden Übergängen zwischen Hochregal und Vorzone den Sauerstoffaustausch auf ein Minimum. Zusätzlich verfügt das Hochregallager in Silobauweise über eine dichte Außenfassade. Die computerunterstützte Blower-Door-Messung ergab einen in Unter- und Überdruck gemittelten n50-Wert von 0,03 Luftwechselrate pro Stunde.
Wegweisend: State-of-the-Art-Logistik Made in Germany
Das neue Fahrrad-Werk von KETTLER Alu-Rad in St. Ingbert führt eindrucksvoll vor Augen, wie modernste Intralogistik heute funktioniert. UBH hat das Raumangebot mit intelligenter Prozessautomation optimal ausgenutzt und die Effizienz nachhaltig erhöht. Innovative Einzellösungen im Kontext einer flächendeckenden State-of-the-Art-Gesamtlösung haben ein Leuchtturmprojekt geschaffen, das zeigt, wie innovative Intralogistik Wertschöpfung steigert und Deutschland damit auch als Produktionsstandort attraktiv hält. Automation vom Feinsten für Fahrräder, die Menschen bewegen, kann so als Vorbild dienen für viele weitere Branchen.
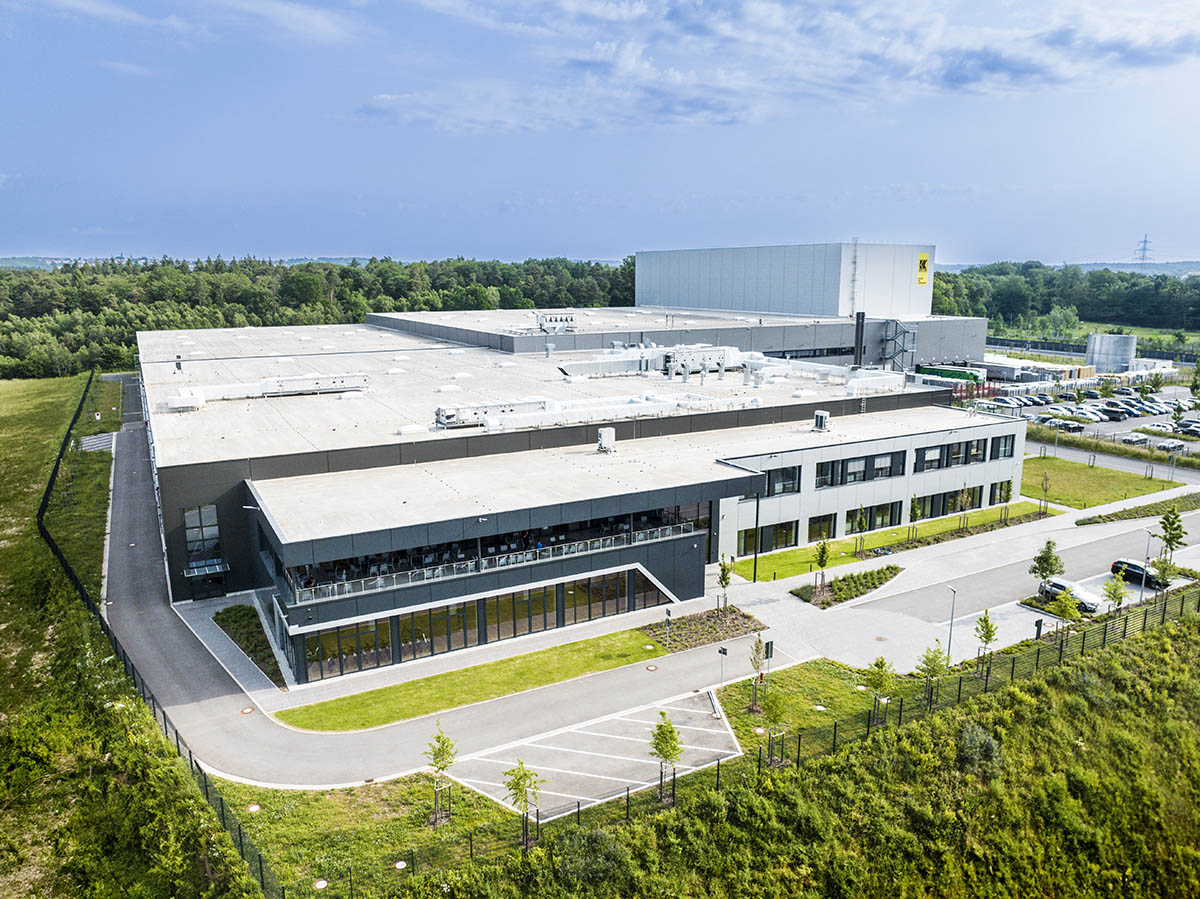
KETTLER Alu-Rad St. Ingbert
LogicsAI: KI-gesteuerter Materialflussrechner im Echteinsatz
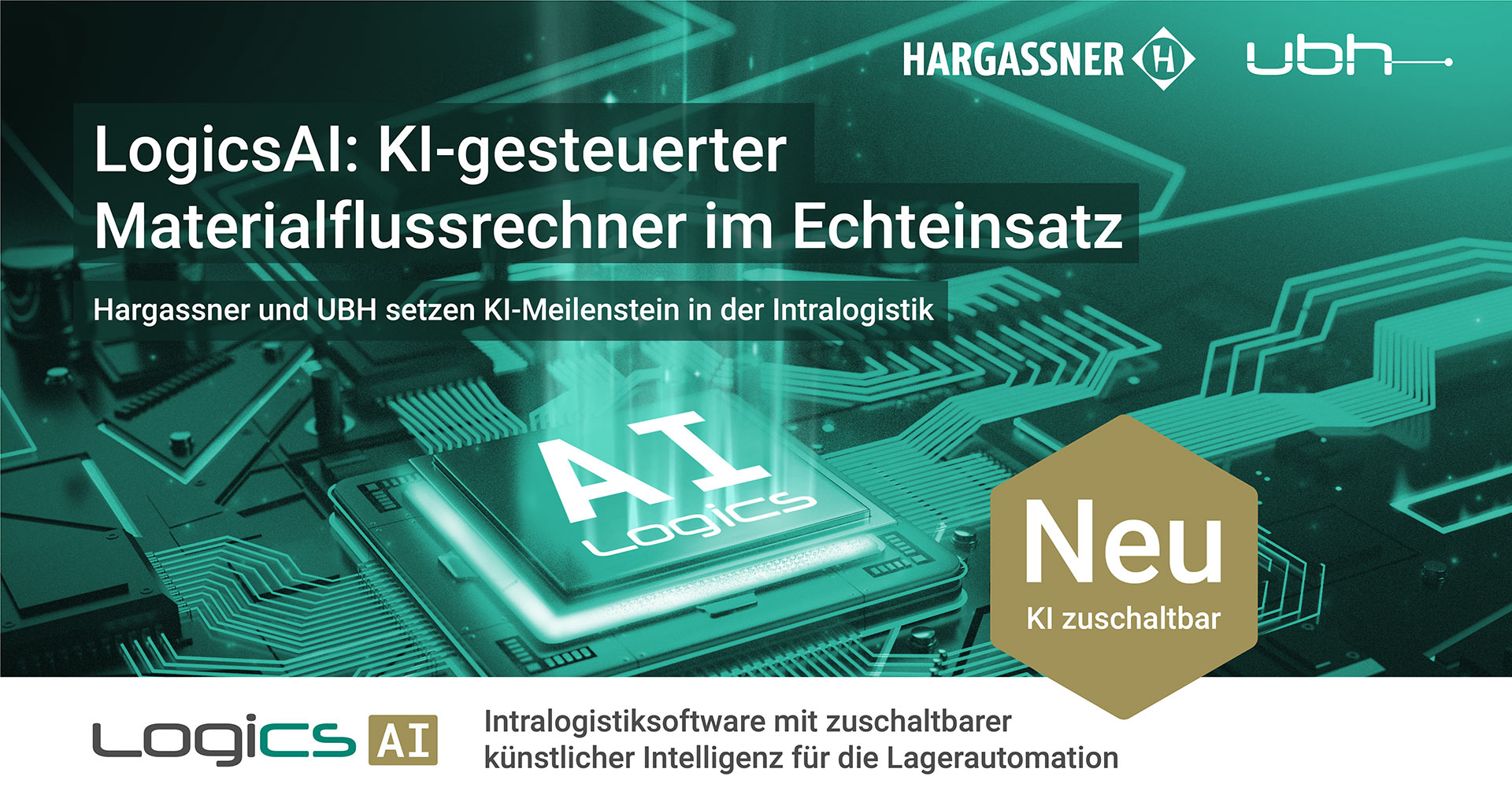
Das österreichische Vorzeigeunternehmen Hargassner und die UBH SOFTWARE & ENGINEERING GmbH aus Deutschland haben die Zusammenarbeit zur Verwirklichung eines großen Schritts in Richtung Industrie 4.0 beschlossen: Der operative Einsatz von künstlicher Intelligenz beim innerbetrieblichen Transport mittels KI-gesteuertem Materialfluss. »Während hardwarebezogene KI- Anwendungen wie bspw. Bewegungsoptimierungen von Robotern oder Bildverarbeitung schon länger im Einsatz sind, haben wir uns darauf konzentriert, vor allem die Systemleistung der bestehenden fördertechnischen Anlagen mittels zuschaltbarem KI-Modul am bestehenden Materialflussrechner zu steigern. Die erzielten Ergebnisse übertreffen die Werte der üblich programmierten Materialfluss- Strategien deutlich. Selbst eine gut durchdachte Programmierung erreicht niemals die Szenario-Umfänge und Dynamik einer KI, die faktisch in Echtzeit analysiert und entscheidet.«, erklärt Gerald Gaberz, Geschäftsführer der UBH. »Wir arbeiten bereits an Erweiterungen unseres Ansatzes und sehen großes Potential für zusätzliche Leistungssteigerungen bei bestehenden Lagerautomationslösungen. Die UBH kann somit Kunden mit bestehenden Anlagen eine Optimierung bieten, die ohne kostspielige Erweiterungen des Maschinenparks oder Gebäudestrukturen auskommt, sozusagen ein „Retrofit Plus.“«
M. Hargassner, Inhaber: »Wir haben uns stets als innovatives Unternehmen verstanden, das seine Kunden mit intelligenten und nachhaltigen Heizlösungen versorgt – die Optimierung unserer internen Logistik mittels KI und damit die weitere Verbesserung unserer Lieferfähigkeit ist die konsequente Fortführung dieser Philosophie!«
»Der Einsatz von künstlicher Intelligenz zur Steigerung der Effizienz in der Logistik ist ein weiterer Schritt in Richtung Industrie 4.0.«, sagt Roland Neubauer, Industrial Engineer bei Hargassner.
Mit dem vierten Quartal ist der effektive Echteinsatz anvisiert.
Kurzporträt Hargassner: Die HARGASSNER Ges mbH mit Sitz in Weng i. I. (Oberösterreich) entwickelt seit 40 Jahren innovative Heizsysteme und beschäftigt 1.150 Mitarbeiter. Das Unternehmen ist führend in Biomasse-Heizsystemen wie Pellets-, Hackgut- und Stückholz-Heizkesseln sowie in Wärmepumpen und Solarkollektoren. Hargassner steht für hohe Effizienz, Zuverlässigkeit und ständige Innovation, um den Energieverbrauch zu senken und Emissionen zu reduzieren. Das Unternehmen beliefert international in 43 Länder nachhaltige Heizlösungen und erneuerbare Energien.